Surface treatment material for abrasion-resistant alloy casting
A technology of surface treatment and wear-resistant alloys, which is applied in the direction of casting molds, casting mold components, casting molding equipment, etc., can solve problems such as unsatisfactory effects, limited coating wear resistance, and complexity of agricultural machinery manufacturing processes. Achieve the effects of simplifying the process, improving wear resistance and corrosion resistance
- Summary
- Abstract
- Description
- Claims
- Application Information
AI Technical Summary
Problems solved by technology
Method used
Examples
Embodiment 1
[0014] A surface treatment material for wear-resistant alloy castings, the treatment material is composed of the following components in parts by weight: 2 parts of aluminum silicate, 2 parts of calcium-based bentonite, 5 parts of diatomite, 2 parts of quartz powder, 3 parts of olivine powder, 1 part of corundum powder, 11 parts of dextrin powder, 2 parts of aluminum sulfate, 11 parts of polyvinyl alcohol, 14 parts of iron oxide powder, 7 parts of n-octanol, 6 parts of nano attapulgite, 5 parts of grass ash, 2 parts of sodium orthophosphate 1 part of diatomite, 2 parts of starch paste, 2 parts of lignosulfonic acid, 3 parts of sodium carboxymethyl cellulose, 4 parts of silica sol, 2 parts of nanoscale ceramic powder, 11 parts of modified graphene, carboxymethyl cellulose 12 parts of sodium methylcellulose, 0.5 parts of iron oxide red powder, 20 parts of two-component polyurethane, 7 parts of hollow glass microspheres, 12 parts of triphenyl phosphite, 2 parts of phenolic resin, ...
Embodiment 2
[0016] A surface treatment material for wear-resistant alloy castings, the treatment material is composed of the following components in parts by weight: 5 parts of aluminum silicate, 5 parts of calcium-based bentonite, 11 parts of diatomite, 5 parts of quartz powder, 7 parts of olivine powder, 3 parts of corundum powder, 14 parts of dextrin powder, 5 parts of aluminum sulfate, 13 parts of polyvinyl alcohol, 16 parts of iron oxide powder, 9 parts of n-octanol, 8 parts of nano attapulgite, 11 parts of grass ash, 5 parts of sodium orthophosphate 9 parts of diatomite, 7 parts of starch paste, 7 parts of lignosulfonic acid, 5 parts of sodium carboxymethyl cellulose, 9 parts of silica sol, 4 parts of nanoscale ceramic powder, 21 parts of modified graphene, carboxymethyl cellulose 23 parts of sodium methylcellulose, 9 parts of mica powder, 0.8 parts of iron oxide red powder, 27 parts of two-component polyurethane, 9 parts of hollow glass microspheres, 15 parts of triphenyl phosphite,...
PUM
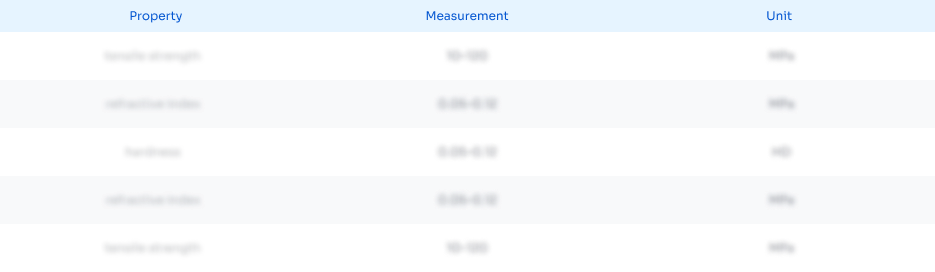
Abstract
Description
Claims
Application Information

- R&D
- Intellectual Property
- Life Sciences
- Materials
- Tech Scout
- Unparalleled Data Quality
- Higher Quality Content
- 60% Fewer Hallucinations
Browse by: Latest US Patents, China's latest patents, Technical Efficacy Thesaurus, Application Domain, Technology Topic, Popular Technical Reports.
© 2025 PatSnap. All rights reserved.Legal|Privacy policy|Modern Slavery Act Transparency Statement|Sitemap|About US| Contact US: help@patsnap.com