Ceramsite fracturing propping agent preparation method
A fracturing proppant and ceramsite technology, applied in the field of drilling aids, can solve the problem that permeability and mechanical properties cannot be improved at the same time, and achieve the effects of improving mechanical properties, toughness and permeability.
- Summary
- Abstract
- Description
- Claims
- Application Information
AI Technical Summary
Problems solved by technology
Method used
Image
Examples
example 1
[0020]Put the peach gum and water in the No. 1 beaker according to the mass ratio of 1:100, stir it with a glass rod for 20 minutes, let it stand for 5 hours to swell, then put the No. , under the condition of 500r / min, heat and stir to dissolve for 60min to obtain the peach glue; place the bamboo fiber in a pulverizer to pulverize, pass through a 120-mesh sieve to obtain bamboo fiber powder, then mix the bamboo fiber powder with a mass fraction of 40 % sodium hydroxide solution is placed in a reaction kettle at a mass ratio of 1:30, and mixed and soaked for 3 hours at a speed of 600r / min and a temperature of 60°C to obtain a soaking mixture, and then filter the soaking mixture to obtain 1 No. 1 filter residue, then wash No. 1 filter residue with glacial acetic acid until the washing liquid is neutral, then place the washed No. 1 filter residue in an oven, and dry it to a moisture content of 8% at a temperature of 110°C to obtain a To process the bamboo fiber powder, place the...
example 2
[0022] Put the peach gum and water in the No. 1 beaker according to the mass ratio of 1:100, stir it with a glass rod for 20 minutes, let it stand for 5 hours to swell, then put the No. , under the condition of 500r / min, heat and stir to dissolve for 60min to obtain the peach glue; place the bamboo fiber in a pulverizer to pulverize, pass through a 120-mesh sieve to obtain bamboo fiber powder, then mix the bamboo fiber powder with a mass fraction of 40 % sodium hydroxide solution is placed in a reaction kettle at a mass ratio of 1:30, and mixed and soaked for 3 hours at a speed of 600r / min and a temperature of 60°C to obtain a soaking mixture, and then filter the soaking mixture to obtain 1 No. 1 filter residue, then wash No. 1 filter residue with glacial acetic acid until the washing liquid is neutral, then place the washed No. 1 filter residue in an oven, and dry it to a moisture content of 8% at a temperature of 110°C to obtain a To process the bamboo fiber powder, place th...
example 3
[0024] Put the peach gum and water in the No. 1 beaker according to the mass ratio of 1:100, stir it with a glass rod for 20 minutes, let it stand for 5 hours to swell, then put the No. , under the condition of 500r / min, heat and stir to dissolve for 60min to obtain the peach glue; place the bamboo fiber in a pulverizer to pulverize, pass through a 120-mesh sieve to obtain bamboo fiber powder, then mix the bamboo fiber powder with a mass fraction of 40 % sodium hydroxide solution is placed in a reaction kettle at a mass ratio of 1:30, and mixed and soaked for 3 hours at a speed of 600r / min and a temperature of 60°C to obtain a soaking mixture, and then filter the soaking mixture to obtain 1 No. 1 filter residue, then wash No. 1 filter residue with glacial acetic acid until the washing liquid is neutral, then place the washed No. 1 filter residue in an oven, and dry it to a moisture content of 8% at a temperature of 110°C to obtain a To process the bamboo fiber powder, place th...
PUM
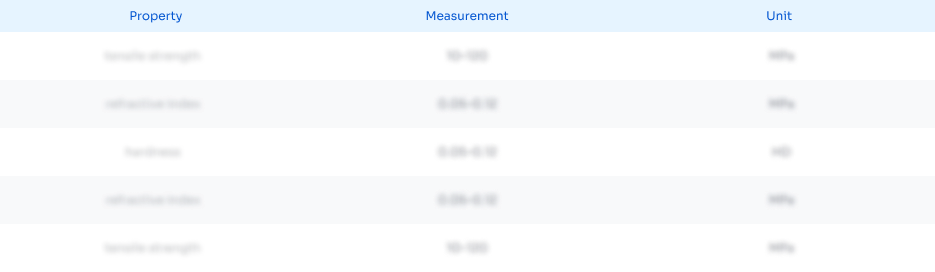
Abstract
Description
Claims
Application Information

- Generate Ideas
- Intellectual Property
- Life Sciences
- Materials
- Tech Scout
- Unparalleled Data Quality
- Higher Quality Content
- 60% Fewer Hallucinations
Browse by: Latest US Patents, China's latest patents, Technical Efficacy Thesaurus, Application Domain, Technology Topic, Popular Technical Reports.
© 2025 PatSnap. All rights reserved.Legal|Privacy policy|Modern Slavery Act Transparency Statement|Sitemap|About US| Contact US: help@patsnap.com