Typical path planning method for 3D (three-dimensional) printing of continuous fiber reinforced composites
A reinforced composite material and continuous fiber technology, which is applied in additive processing, manufacturing auxiliary devices, processing data acquisition/processing, etc., can solve the problems of printing failure of forming components, restricting the performance of forming components, and weak fiber binding force, etc. The effect of overall performance, reduction of molding defects, and improvement of bonding force
- Summary
- Abstract
- Description
- Claims
- Application Information
AI Technical Summary
Problems solved by technology
Method used
Image
Examples
Embodiment Construction
[0025] The present invention will be further described in detail below in conjunction with the accompanying drawings and technical solutions.
[0026] The continuous fiber reinforced material used in the planning method of the present invention is one or more of continuous carbon fiber wire, continuous glass fiber wire, continuous ceramic fiber or continuous silicon carbide fiber, and also includes continuous fiber tow prepared according to special application occasions; the resin used It is one or more of ABS resin, polyamide or polyetheretherketone thermoplastic resin.
[0027] In this embodiment, 1K continuous carbon fiber and nylon are used as raw materials for 3D printing, wherein the continuous carbon fiber is pretreated, and according to the experiment, the minimum angle that can be bent is 13°.
[0028] The flow chart of the path planning method in this embodiment is as follows figure 1 As shown, the specific steps of the planning method are as follows:
[0029]Step ...
PUM
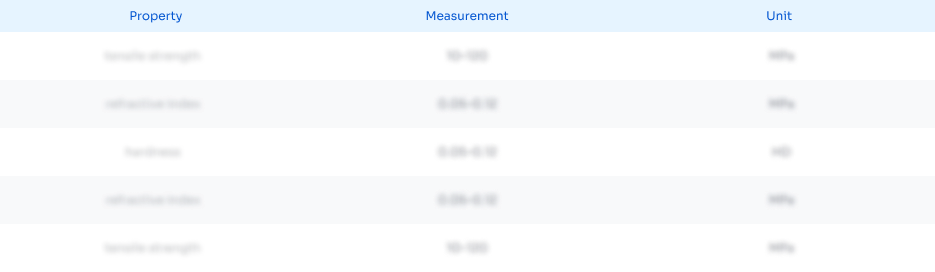
Abstract
Description
Claims
Application Information

- R&D
- Intellectual Property
- Life Sciences
- Materials
- Tech Scout
- Unparalleled Data Quality
- Higher Quality Content
- 60% Fewer Hallucinations
Browse by: Latest US Patents, China's latest patents, Technical Efficacy Thesaurus, Application Domain, Technology Topic, Popular Technical Reports.
© 2025 PatSnap. All rights reserved.Legal|Privacy policy|Modern Slavery Act Transparency Statement|Sitemap|About US| Contact US: help@patsnap.com