Technology for comprehensively treating heavy oil produced in hydration-method cyclohexanone production process
A technology for comprehensive treatment and cyclohexanone is applied in the field of heavy oil produced in the process of comprehensive treatment of cyclohexanone by hydration method. , the effect of reducing pollution
- Summary
- Abstract
- Description
- Claims
- Application Information
AI Technical Summary
Problems solved by technology
Method used
Image
Examples
Embodiment 1
[0031] A process for comprehensively treating the heavy oil produced in the hydration method for producing cyclohexanone, comprising the steps of:
[0032] The by-product heavy oil 2000kg / h of the hydration method cyclohexanone plant is sent to the primary fractionation tower T-101. It is -0.08MPaG, and the number of theoretical plates is 40; the separation of the tower bottom of the primary separation tower T-101 obtains a component with a boiling point greater than phenol, which is sent to the intermediate component tower T-105 through the primary separation tower tank pump P-101, and the Phenol and light components with a boiling point lower than phenol are obtained from the top separation, and after passing through the condenser E-102 of the primary fractionation column and the reflux tank V-101 of the primary fractionation column, they are sent to the azeotropic distillation column T by the reflux pump P-102 of the primary fractionation column -102 Central.
[0033]The a...
Embodiment 2
[0040] A process for comprehensively treating heavy oil produced in the process of producing cyclohexanone through hydration, comprising the following steps: the process is the same as in Example 1.
[0041] The by-product heavy oil 3750kg / h of the hydration method cyclohexanone plant is sent to the primary fractionation tower T-101. It is -0.075MPaG, and the number of theoretical plates is 40; Azeotropic rectification column T-102 adopts the binary mixture of acetophenone and benzoic acid as entrainer, and flow rate is 3000kg / h, and wherein benzoic acid content is 10wt%, altogether The reflux ratio of the boiling distillation column T-102 is 4.8, the temperature at the top of the column is 61°C, the temperature at the bottom of the column is 101°C, the pressure is -0.097MPaG, and the number of theoretical plates is 40; the reflux ratio of the cyclohexanone column T-103 is 6. The temperature at the top of the tower is 67°C, the temperature at the bottom of the tower is 85°C, t...
Embodiment 3
[0044] A process for comprehensively treating heavy oil produced in the process of producing cyclohexanone through hydration, comprising the following steps: the process is the same as in Example 1.
[0045] The 4500kg / h of heavy oil produced by the hydration method cyclohexanone plant is sent to the primary fractionation tower T-101. It is -0.075MPaG, and the number of theoretical plates is 40; Azeotropic rectification tower T-102 adopts the binary mixture of acetophenone and benzoic acid as entrainer, and flow rate is 3600kg / h, and wherein benzoic acid content is 15wt%, altogether The reflux ratio of the boiling distillation column T-102 is 2, the temperature at the top of the column is 64°C, the temperature at the bottom of the column is 100°C, the pressure is -0.097MPaG, and the number of theoretical plates is 40; the reflux ratio of the cyclohexanone column T-103 is 3. The temperature at the top of the tower is 67°C, the temperature of the tower bottom is 85°C, the pressu...
PUM
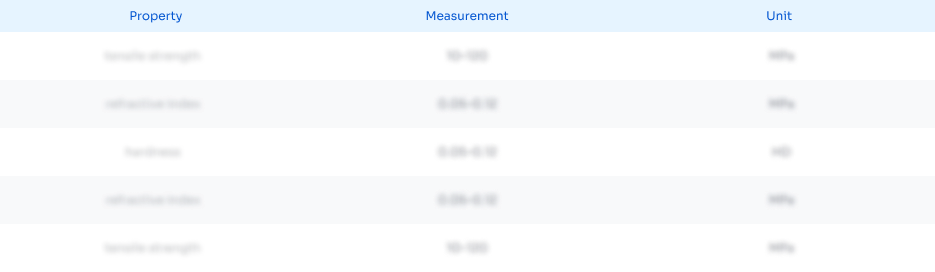
Abstract
Description
Claims
Application Information

- Generate Ideas
- Intellectual Property
- Life Sciences
- Materials
- Tech Scout
- Unparalleled Data Quality
- Higher Quality Content
- 60% Fewer Hallucinations
Browse by: Latest US Patents, China's latest patents, Technical Efficacy Thesaurus, Application Domain, Technology Topic, Popular Technical Reports.
© 2025 PatSnap. All rights reserved.Legal|Privacy policy|Modern Slavery Act Transparency Statement|Sitemap|About US| Contact US: help@patsnap.com