Method for enhancing strength of high-aluminum preform
A prefabricated, high-aluminum technology, which is applied in the field of prefabricated parts processing, can solve the problems of difficulty in transportation and use of prefabricated parts, reduce the slag resistance performance of prefabricated parts, reduce the service life of refractory materials, etc., so as to improve the slag corrosion resistance. , The effect of reducing operating costs and improving service life
- Summary
- Abstract
- Description
- Claims
- Application Information
AI Technical Summary
Problems solved by technology
Method used
Image
Examples
Embodiment 1
[0034] The method for enhancing the strength of high-aluminum prefabricated parts is carried out according to the following steps:
[0035] 1) First raise the water temperature to 60-70°C, then add the magnesium sulfate heptahydrate solute calculated according to the solubility into the water, stir until there is no solvent at the bottom of the solution, then let the water temperature cool down to room temperature naturally, and set aside;
[0036] 2) Ladle prefabricated bricks (aluminum content 85wt%) are neatly stacked on special pallets and naturally cured for 3-4 days;
[0037] 3) Then soak it in a supersaturated solution of magnesium sulfate heptahydrate until the air bubbles on the surface of the prefabricated brick disappear. The whole process takes 3 hours;
[0038] 4) Put the prefabricated bricks soaked in the solution into a low-temperature baking kiln at 150°C and bake for 25 hours. After leaving the kiln, they can become finished products.
Embodiment 2
[0040] The method for enhancing the strength of high-aluminum prefabricated parts is carried out according to the following steps:
[0041] 1) First raise the water temperature to 60-70°C, then add the magnesium sulfate heptahydrate solute calculated according to the solubility into the water, and add lanthanum oxide at the same time, the amount of lanthanum oxide is 10wt% of the magnesium sulfate heptahydrate, and stir until the solution There is no solvent at the bottom, the stirring rate is 200rpm, and then let the water cool down to room temperature naturally to form a soaking liquid for later use;
[0042] 2) Ladle prefabricated bricks (92wt% aluminum content) are neatly stacked on special pallets, and naturally cured for 3-4 days;
[0043] 3) Then soak it in the soaking solution until the air bubbles on the surface of the prefabricated brick disappear, and the whole process takes 4 hours;
[0044] 4) Put the whole prefabricated brick soaked in the solution into a low-te...
Embodiment 3
[0046] The method for enhancing the strength of high-aluminum prefabricated parts is carried out according to the following steps:
[0047] 1) First raise the water temperature to 60-70°C, then add the magnesium sulfate heptahydrate solute calculated according to the solubility into the water, and add cerium oxide at the same time, the amount of cerium oxide is 20wt% of the magnesium sulfate heptahydrate, and stir until the solution There is no solvent at the bottom, the stirring rate is 300rpm, and then let the water cool down to room temperature naturally to form a soaking liquid for later use;
[0048] 2) Ladle prefabricated bricks (with an aluminum content of 90wt%) are neatly stacked on special pallets, and naturally cured for 3-4 days;
[0049] 3) Then soak it in the soaking solution until the air bubbles on the surface of the prefabricated brick disappear, and the whole process takes 4 hours;
[0050] 4) Put the prefabricated bricks soaked in the solution into a low-temp...
PUM
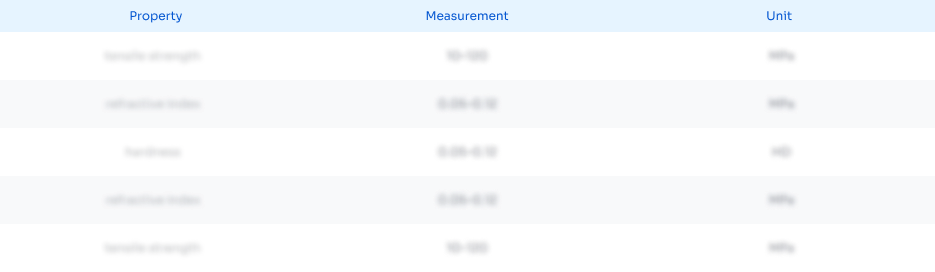
Abstract
Description
Claims
Application Information

- R&D Engineer
- R&D Manager
- IP Professional
- Industry Leading Data Capabilities
- Powerful AI technology
- Patent DNA Extraction
Browse by: Latest US Patents, China's latest patents, Technical Efficacy Thesaurus, Application Domain, Technology Topic, Popular Technical Reports.
© 2024 PatSnap. All rights reserved.Legal|Privacy policy|Modern Slavery Act Transparency Statement|Sitemap|About US| Contact US: help@patsnap.com