Structure and process integrated design method for FRP structural part
A design method and technology of structural parts, applied in the direction of design optimization/simulation, calculation, special data processing applications, etc., can solve the problems of lack of theoretical methods, inability to guarantee the optimal structure of the design structure, etc., achieve high economic benefits, and improve optimal design Effect of efficiency, high material utilization
- Summary
- Abstract
- Description
- Claims
- Application Information
AI Technical Summary
Problems solved by technology
Method used
Image
Examples
Embodiment
[0105] This embodiment performs high-precision finite element modeling on a certain engine cover, such as figure 2 shown. In the bonnet, the inner and outer panels are made of carbon fiber reinforced composite material (CFRP), and the rest of the reinforcement panels are still made of original steel materials.
[0106] Select 0°, ±45°, and 90° as the four alternative angles of the CFRP engine cover, and generate the constitutive matrix of the four alternative angles. The CFRP engine hood inner panel is selected as the design domain for optimal design. The initial design of the inner panel of the CFRP engine hood adopts 16 layers of CFRP unidirectional belt laminate, and the outer panel is composed of 5 layers of CFRP. Among them, the outermost layer of the outer panel is laminated with orthogonal woven fabric for the sake of appearance.
[0107] The finite element analysis is carried out for the torsion, forward bending, backward bending and lateral stiffness conditions of ...
PUM
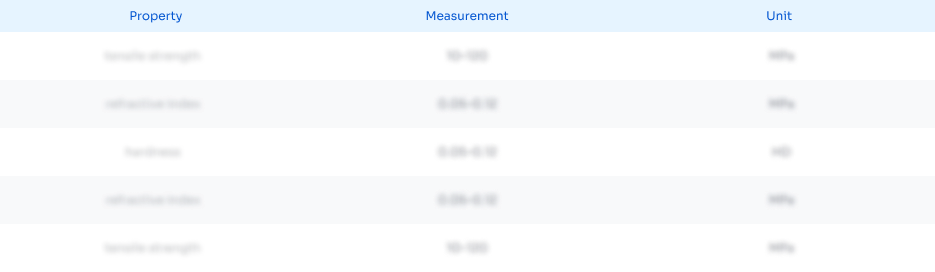
Abstract
Description
Claims
Application Information

- R&D Engineer
- R&D Manager
- IP Professional
- Industry Leading Data Capabilities
- Powerful AI technology
- Patent DNA Extraction
Browse by: Latest US Patents, China's latest patents, Technical Efficacy Thesaurus, Application Domain, Technology Topic, Popular Technical Reports.
© 2024 PatSnap. All rights reserved.Legal|Privacy policy|Modern Slavery Act Transparency Statement|Sitemap|About US| Contact US: help@patsnap.com