Method and device for continuous preparing of corrosion-resisting joist steel through hot dip aluminum plating method
A technology of hot-dip aluminum plating and I-beam, applied in hot-dip plating process, metal material coating process, coating, etc., can solve problems such as difficulties, affecting the surface quality of strip steel, friction and scratches on steel surface, etc., and achieve Energy saving, impact reduction, uniform thickness effect
- Summary
- Abstract
- Description
- Claims
- Application Information
AI Technical Summary
Problems solved by technology
Method used
Image
Examples
Embodiment 1
[0040] A kind of method that the present invention proposes can prepare the aluminized I-beam of high corrosion resistance performance, and concrete operation step is:
[0041] (1) Pretreatment of the I-beam: use sandpaper to polish off the oxide layer on the surface of the I-beam sample 1, pickle with hydrochloric acid, degrease with alcohol and acetone, and dry it with cold wind;
[0042] (2) Preparation of molten aluminum in the reserve molten pool 8: Add high-purity aluminum ingots and a certain amount of rare earth elements into the reserve molten pool, turn on the power to heat, melt it, and keep it within a certain temperature range to make the molten aluminum Have a certain degree of superheat;
[0043] (3) Preparation of the aluminum coating 21: open the preheating furnace 4, preheat the I-beam sample 1, and control its temperature at 200-500° C., open the electromagnetic seal valve through the inductor 10 of the electromagnetic valve, and store The rare earth-contai...
Embodiment 2
[0047] Add 100kg of high-purity aluminum ingots and 0.4kg of cerium into the reserve molten pool 8, turn on the preheating furnace 4, keep the temperature at 690-900°C, open the electromagnetic sealing valve through the sensor 10 of the electromagnetic valve, and turn on the conveying roller at the same time One 2 and conveying roller two 3, at the same time, use the hydraulic jack 5 to transfer the molten aluminum in the reserve molten pool 8 into the dipping pool 11 through the catheter 13, and control the temperature at 750±20°C. The Q235 I-beam with a size of 100×63×4.5 is controlled at a transmission speed of 10m / min. Under the viscosity of the melt, a layer of aluminum coating 21 is covered on the surface of the I-beam sample 1, and then passes through the upper end of the dipping pool 11. Air knife 14 and air knife 2 15 with a preheating temperature of about 60°C and compressed gas of high-purity argon are used to spray the coating surface, and the air knife 14 and air k...
PUM
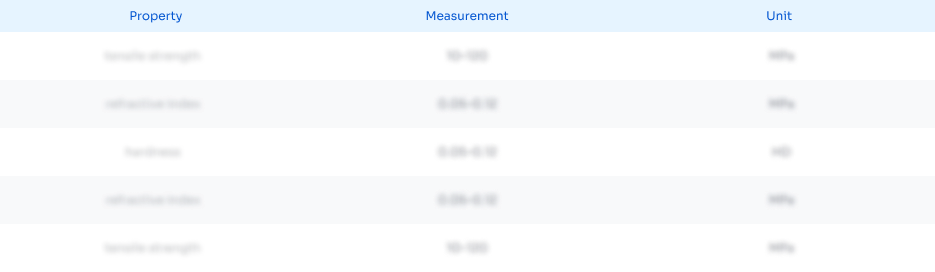
Abstract
Description
Claims
Application Information

- R&D
- Intellectual Property
- Life Sciences
- Materials
- Tech Scout
- Unparalleled Data Quality
- Higher Quality Content
- 60% Fewer Hallucinations
Browse by: Latest US Patents, China's latest patents, Technical Efficacy Thesaurus, Application Domain, Technology Topic, Popular Technical Reports.
© 2025 PatSnap. All rights reserved.Legal|Privacy policy|Modern Slavery Act Transparency Statement|Sitemap|About US| Contact US: help@patsnap.com