A kind of plastic optical fiber core material and its preparation method and application
A plastic optical fiber and core layer technology, which is applied in the field of polymer materials, can solve the problems of poor heat resistance, chemical corrosion resistance and aging resistance, restricting the large-scale application of plastic optical fibers, and large attenuation of plastic optical fibers, etc., to achieve high optical performance , reduced brittleness, improved aging resistance
- Summary
- Abstract
- Description
- Claims
- Application Information
AI Technical Summary
Problems solved by technology
Method used
Image
Examples
Embodiment 1
[0038] The composition for preparing plastic optical fiber core material consists of the following components in parts by mass: 88 parts of methyl methacrylate, 4 parts of methyl acrylate, 8 parts of trifluoroethyl methacrylate, di-tert-peroxide 0.018 parts of butyl, 0.02 parts of n-octyl mercaptan.
[0039] The method for preparing a plastic optical fiber core layer material by using the above-mentioned composition comprises the following steps: purifying the above-mentioned substances, after the purity reaches 99.999%, mixing them into a mixed solution according to the above-mentioned parts by mass, and keeping the mixed solution in a stirring state after mixing , inject the mixed solution into a qualified polymerization reactor that has been replaced by nitrogen to carry out the polymerization reaction. During the reaction, the temperature of the reactor was controlled at 160° C. to 185° C., the reaction pressure was controlled at 4.0 MPa, and the reaction time was 70 minut...
Embodiment 2
[0041] The composition for preparing plastic optical fiber core material consists of the following components in parts by mass: 85 parts of methyl methacrylate, 5 parts of methyl acrylate, 10 parts of trifluoroethyl methacrylate, di-tert-peroxide 0.018 parts of butyl, 0.02 parts of n-octyl mercaptan.
[0042] The method for preparing a plastic optical fiber core layer material using the above-mentioned composition comprises the following steps: purifying the above-mentioned various raw materials, after the purity reaches 99.999%, mixing them into a mixed solution according to the above-mentioned parts by mass, and keeping the mixed solution under stirring after mixing state, inject the mixed solution into a qualified polymerization reactor that has been replaced by nitrogen to carry out the polymerization reaction. During the reaction, the temperature of the reactor was controlled at 160° C. to 185° C., the reaction pressure was controlled at 4.2 MPa, and the reaction time was...
Embodiment 3
[0044]The composition for preparing plastic optical fiber core material consists of the following components in parts by mass: 83 parts of methyl methacrylate, 6 parts of methyl acrylate, 11 parts of trifluoroethyl methacrylate, di-tert-peroxide 0.018 parts of butyl, 0.02 parts of n-octyl mercaptan.
[0045] The method for preparing a plastic optical fiber core layer material by using the above-mentioned composition comprises the following steps: purifying the above-mentioned raw materials, after the purity reaches 99.999%, mixing them into a mixed solution according to the above-mentioned parts by mass, and keeping the mixed solution in a stirring state after mixing , inject the mixed solution into a qualified polymerization reactor that has been replaced by nitrogen to carry out the polymerization reaction. During the reaction, the temperature of the reactor was controlled at 160° C. to 185° C., the reaction pressure was controlled at 4.2 MPa, and the reaction time was 75 mi...
PUM
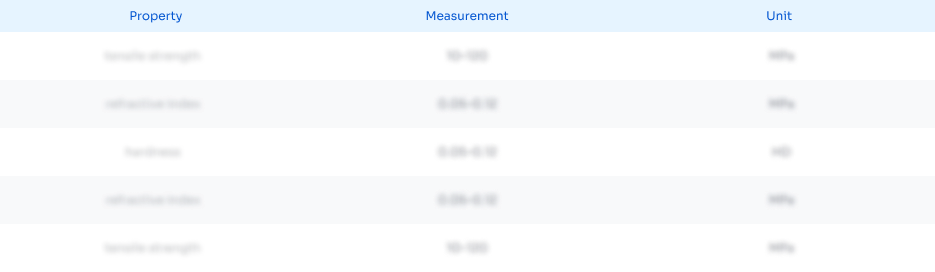
Abstract
Description
Claims
Application Information

- R&D Engineer
- R&D Manager
- IP Professional
- Industry Leading Data Capabilities
- Powerful AI technology
- Patent DNA Extraction
Browse by: Latest US Patents, China's latest patents, Technical Efficacy Thesaurus, Application Domain, Technology Topic, Popular Technical Reports.
© 2024 PatSnap. All rights reserved.Legal|Privacy policy|Modern Slavery Act Transparency Statement|Sitemap|About US| Contact US: help@patsnap.com