Resin precoated sand and preparation method thereof
A technology of resin coating and coating sand, which is applied in the field of foundry molding to achieve the effects of low expansion characteristics, reduced veining, and good coating effect.
- Summary
- Abstract
- Description
- Claims
- Application Information
AI Technical Summary
Problems solved by technology
Method used
Image
Examples
Embodiment 1
[0043] A preparation method of resin-coated sand, comprising the following steps:
[0044] (1) Aggregate: 78.5% of calcined sand and 21.5% of regenerated sand are used to prepare aggregate for coating, which contains 49.4% of low-temperature phase β phase, 40.4% of high-temperature phase α phase, 5.7% of orthoclase, and 5.7% of orthoclase. Plagioclase 4.5%.
[0045] The reclaimed sand includes the following:
[0046] A. Regenerated sand derived from the waste sand formed by phenolic resin-coated sand applied to non-ferrous metal, ferrous metal and cast steel casting by thermomechanical regeneration process;
[0047] B. Regenerated sand obtained by thermo-mechanical regeneration process after applying cold core box resin sand to waste sand formed by casting of non-ferrous and ferrous metals;
[0048] C, derived from the regenerated sand prepared by the thermomechanical regeneration process after the furan resin sand is applied to the waste sand formed by non-ferrous ferrous m...
Embodiment 2
[0056] The difference from Example 1 is that in step (1), 100% of regenerated sand is selected as the aggregate for coating, which contains 0% of low-temperature phase β phase, 95.7% of high-temperature phase α phase, and 4.3% of orthoclase. %, containing plagioclase 0%; in step (2), the amount of thermoplastic resin accounts for 3.5% of the total aggregate amount; in step (3), the aggregate is heated to 140 ° C, the viscosity of thermoplastic resin at 132 ° C Add to the aggregate at 400 cp, add curing agent urotropine accounting for 20% of the resin, and calcium stearate as a release agent accounting for 0.2% of the aggregate to mix sand. The speed of sand mixing is 80r / min. After mixing uniformly, the resin-coated sand is obtained by crushing, screening and cooling, and the total ignition loss of the prepared coated sand is controlled to be 4.5%. Example 3
Embodiment 3
[0057] The difference from Example 1 is that in step (1), 10% of scrubbing sand, 25% of calcined sand, and 65% of regenerated sand are used as aggregates for coating, which contain 25.1% of low-temperature phase β phase and 25.1% of high-temperature phase. α phase 66.3%, orthoclase 7.2%, plagioclase 1.4%; in step (2), the average degree of polymerization of the thermoplastic resin is 8-15, the number-average molecular weight distribution is 800-16000, and the weight-average molecular weight distribution is 900-20,000, wherein the ratio of number-average molecular weight to weight-average molecular weight is between 1.3 and 4, and the amount of thermoplastic resin accounts for 1% of the total aggregate amount; in step (3), the aggregate is heated to 140 ° C, and the thermoplastic resin is in When the viscosity at 130℃ is 450cp, it is added to the aggregate, and the curing agent urotropine, which accounts for 18% of the resin, and the release agent calcium stearate, which account...
PUM
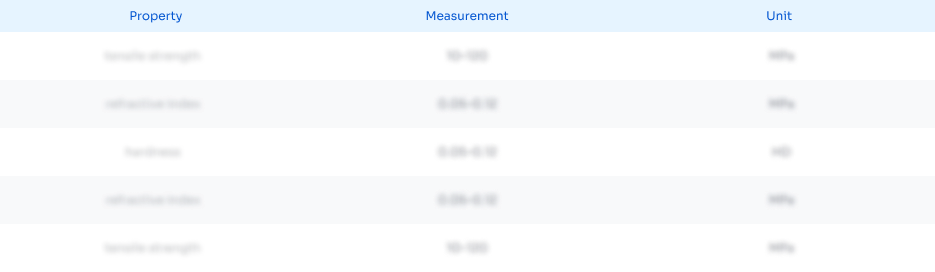
Abstract
Description
Claims
Application Information

- Generate Ideas
- Intellectual Property
- Life Sciences
- Materials
- Tech Scout
- Unparalleled Data Quality
- Higher Quality Content
- 60% Fewer Hallucinations
Browse by: Latest US Patents, China's latest patents, Technical Efficacy Thesaurus, Application Domain, Technology Topic, Popular Technical Reports.
© 2025 PatSnap. All rights reserved.Legal|Privacy policy|Modern Slavery Act Transparency Statement|Sitemap|About US| Contact US: help@patsnap.com