Method for preparing alkane isomerization catalyst
A technology of alkane isomerization and catalyst, which is applied in the field of catalyst preparation, can solve the problems of reducing the yield of diesel oil, achieve the effects of suppressing side reactions and high resistance to sulfide poisoning
- Summary
- Abstract
- Description
- Claims
- Application Information
AI Technical Summary
Problems solved by technology
Method used
Image
Examples
Embodiment 1
[0033] Take 0.46mmol trimethoxymercaptopropylsilane and 86mmol NaOH, add them to 7.25mL deionized water, and stir at room temperature for 12h. Add 0.038mmol H 2 PtCl 6 ·6H 2 O, stirred at room temperature for 0.5h. Then add 10mmol SiO 2 , stirred at 80°C for 0.5h, and cooled to room temperature. Add 2.09mol / L NaAlO dropwise 2 Solution 7.25mL, continue to stir for 4h.
[0034] The obtained material was put into a stainless steel reaction kettle lined with polytetrafluoroethylene, and subjected to constant temperature and dynamic hydrothermal crystallization reaction at 100° C. for 12 hours. The solid obtained from the reaction was taken out, washed and dried to obtain a Pt@SOD catalytic material encapsulated with Pt nanoclusters.
[0035] figure 1 The XRD patterns of the as-prepared Pt@SOD catalytic materials are given. It can be seen from the figure that the prepared Pt@SOD catalytic material shows the characteristic diffraction peaks of SOD, and the crystallization ...
Embodiment 2
[0039] Take 0.23mmol trimethoxymercaptopropylsilane and 86mmol NaOH, add them to 7.25mL deionized water, and stir at room temperature for 12h. Add 0.019mmol Pd(NH 3 ) 4 Cl 2 , stirred at room temperature for 0.5h. Then add 10mmol SiO 2 , stirred at 80°C for 0.5h, and cooled to room temperature. Add 2.09mol / L NaAlO dropwise 2 Solution 7.25mL, continue to stir for 4h.
[0040] The obtained material was put into a stainless steel reaction kettle lined with polytetrafluoroethylene, and subjected to constant temperature and dynamic hydrothermal crystallization reaction at 100° C. for 12 hours. The solid obtained from the reaction was taken out, washed and dried to obtain a Pd@SOD catalyst encapsulated with Pd nanoclusters.
[0041] Take 0.2g of Pd@SOD catalyst, mix it mechanically with 0.2g of HBeta zeolite, pulverize it, press it into tablets, then crush it, and sieve to get 40-60 mesh particles, put them in a continuous flow fixed-bed reaction device, in 50mL / min of H 2 T...
Embodiment 3
[0043] Take 0.46mmol trimethoxymercaptopropylsilane and 86mmol NaOH, add them to 7.25mL deionized water, and stir at room temperature for 12h. Add 0.038mmol H 2 IrCl 6 , stirred at room temperature for 0.5h. Then add 10mmol SiO 2 , stirred at 80°C for 0.5h, and cooled to room temperature. Add 2.09mol / L NaAlO dropwise 2 Solution 7.25mL, continue to stir for 4h.
[0044] The obtained material was put into a stainless steel reaction kettle lined with polytetrafluoroethylene, and subjected to constant temperature and dynamic hydrothermal crystallization reaction at 100° C. for 12 hours. The solid obtained from the reaction was taken out, washed and dried to obtain an Ir@SOD catalyst encapsulated with Ir nanoclusters.
[0045] Take 0.2g of Ir@SOD catalyst, mix it mechanically with 0.2g of HZSM-5 zeolite, pulverize it, press it into tablets, then crush it, sieve and take 40-60 mesh particles, put them in a continuous-flow fixed-bed reaction device, at 50mL / min H 2 The temper...
PUM
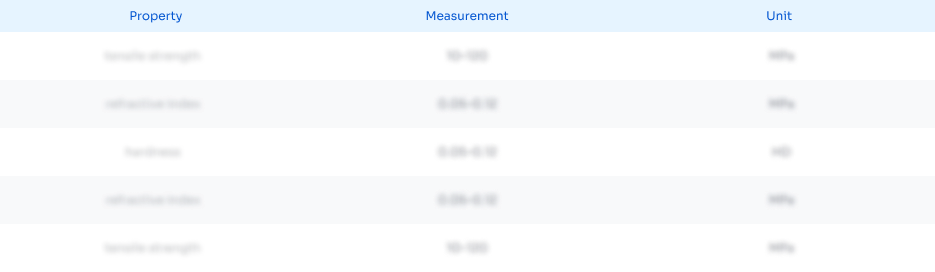
Abstract
Description
Claims
Application Information

- Generate Ideas
- Intellectual Property
- Life Sciences
- Materials
- Tech Scout
- Unparalleled Data Quality
- Higher Quality Content
- 60% Fewer Hallucinations
Browse by: Latest US Patents, China's latest patents, Technical Efficacy Thesaurus, Application Domain, Technology Topic, Popular Technical Reports.
© 2025 PatSnap. All rights reserved.Legal|Privacy policy|Modern Slavery Act Transparency Statement|Sitemap|About US| Contact US: help@patsnap.com