A kind of method of diamond film surface graphitization
A technology of diamond film and graphitization, which is applied in the direction of gaseous chemical plating, metal material coating process, structural parts, etc., can solve the problems of poor electrical conductivity, decreased thermal conductivity performance, and decreased diamond quality, achieving high energy density and good The effect of thermal conductivity
- Summary
- Abstract
- Description
- Claims
- Application Information
AI Technical Summary
Problems solved by technology
Method used
Image
Examples
Embodiment 1
[0019] (1) Cleaning: Sonicate the Ti sheet in acetone, ethanol and deionized aqueous solution for 15 minutes and dry it;
[0020] (2) Pretreatment: Place the cleaned Ti sheet in a 2mol / L dilute HCl solution for 10 minutes to remove the surface oxide layer, wash it repeatedly with deionized water until neutral, and dry it with nitrogen;
[0021] (3) The above-mentioned Ti sheet was ultrasonically treated in diamond powder suspension for 30 min, followed by ultrasonic cleaning in ethanol for 5 min, and dried with nitrogen gas for use.
[0022] (4) The substrate to be used is placed on the sample stage in the hot wire chemical vapor deposition equipment, and the background vacuum is pumped to 1×10 - 3 Above Pa. Introduce hydrogen, and adjust the pumping speed of the vacuum pump to maintain the pressure in the reaction chamber at 50 Torr. The filament material is tantalum wire, heated to 2100±100°C, the substrate temperature is 800±150°C, and the substrate surface is etched with...
Embodiment 2
[0025] (1) Cleaning: Sonicate the Si sheet in acetone, ethanol and deionized water solution for 15 minutes and dry it;
[0026] (2) Pretreatment: place the cleaned Si sheet in a 2mol / L dilute HCl solution for 10 minutes to remove the surface oxide layer, wash it repeatedly with deionized water until neutral, and dry it with nitrogen;
[0027] (3) The above-mentioned Si sheet was placed in a diamond powder suspension for ultrasonic treatment for 30 min, followed by ultrasonic cleaning in ethanol for 5 min, and dried with nitrogen gas for use.
[0028] (4) The substrate to be used is placed on the sample stage in the hot wire chemical vapor deposition equipment, and the background vacuum is pumped to 1×10 - 3 Above Pa. Introduce hydrogen, and adjust the pumping speed of the vacuum pump to maintain the pressure in the reaction chamber at 40Torr, the filament material is tantalum wire, heated to 2100±100°C, the substrate temperature is 800±150°C, and the substrate surface is etc...
PUM
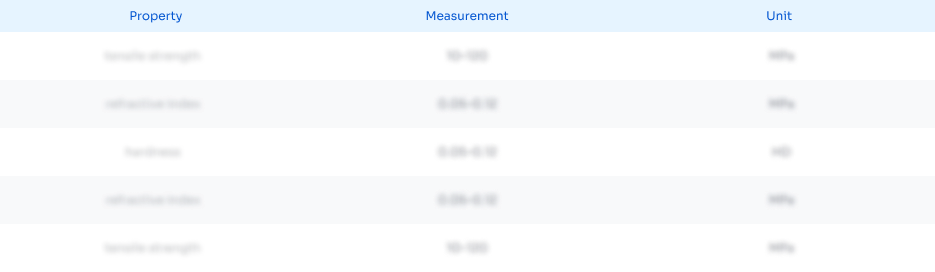
Abstract
Description
Claims
Application Information

- R&D
- Intellectual Property
- Life Sciences
- Materials
- Tech Scout
- Unparalleled Data Quality
- Higher Quality Content
- 60% Fewer Hallucinations
Browse by: Latest US Patents, China's latest patents, Technical Efficacy Thesaurus, Application Domain, Technology Topic, Popular Technical Reports.
© 2025 PatSnap. All rights reserved.Legal|Privacy policy|Modern Slavery Act Transparency Statement|Sitemap|About US| Contact US: help@patsnap.com