Preparation method of intelligent glass anode electrochromic layer coating material
An anodic electrochromic and smart glass technology, applied in metal material coating process, coating, manufacturing tools, etc., can solve the problems of high cost of smart glass, increased frequency of nickel target replacement, slow industrialization progress, etc., to achieve Effects of improving chemical stability, reducing film roughness, and improving applicability
- Summary
- Abstract
- Description
- Claims
- Application Information
AI Technical Summary
Problems solved by technology
Method used
Image
Examples
Embodiment 1
[0018] A method for preparing an anode electrochromic layer coating material for smart glass, using pure nickel oxide powder, adding 68wt% zirconia balls, 30wt% pure water and 2wt% dispersant, grinding and mixing fully, the time is 36 hours, The formed slurry is poured into a three-inch porous mold, and after 24 hours of drying, the low-density green body of the oxide is formed by demolding, and then sintered in a vacuum sintering furnace at 1300°C for 5 hours, with a vacuum degree of 2000mmHg. Form a high-density target body for sputtering, cut and grind the surface into a three-inch target; then put the required coated glass substrate into the sputtering chamber, and vacuum the background of the sputtering chamber The pressure is pumped to 0.8×10 -5 After torr, a mixed gas of argon and oxygen is introduced, the volume ratio of oxygen in the mixed gas is 3%, and the mixed gas is passed through the throttle valve to control the working pressure of the sputtering chamber to be ...
Embodiment 2
[0021] A method for preparing an anode electrochromic layer coating material for smart glass, using pure nickel oxide powder, adding a second oxide to the nickel oxide, then adding 68wt% zirconia balls, 30wt% pure water and 2wt% Dispersant, grinding and mixing, the time is 24 hours, the formed slurry is poured into a three-inch porous mold, after 24 hours of drying, the low-density green body of the oxide is formed by demolding, and then passed through the vacuum sintering furnace Sintering at 1100°C for 3 hours, with a vacuum of 400mmHg, to form a high-density target body for sputtering, which is cut and ground into a three-inch target; then put the required glass substrate into the sputtering chamber, Use the vacuum pumping system to pump the background pressure of the sputtering chamber to 0.7×10 -5 After torr, the mixed gas of argon and oxygen is introduced, the volume ratio of oxygen in the mixed gas is 2%, and the working pressure of the sputtering chamber is controlled ...
Embodiment 3
[0025] A method for preparing an anode electrochromic layer coating material for smart glass, using pure nickel oxide powder, adding a second oxide to the nickel oxide, then adding 68wt% zirconia balls, 30wt% pure water and 2wt% Dispersant, grinding and mixing, the time is 36 hours, the formed slurry is poured into a three-inch porous mold, after 24 hours of drying, the low-density green body of the oxide is formed by demolding, and then passed through the vacuum sintering furnace Sintering at 1300°C for 5 hours, with a vacuum of 2000mmHg, to form a high-density target body for sputtering, which is cut and ground into a three-inch target; then put the required glass substrate into the sputtering chamber, Use the vacuum pumping system to pump the background pressure of the sputtering chamber to 0.8×10 -5 After torr, a mixed gas of argon and oxygen is introduced, the volume ratio of oxygen in the mixed gas is 3%, and the mixed gas is passed through the throttle valve to control ...
PUM
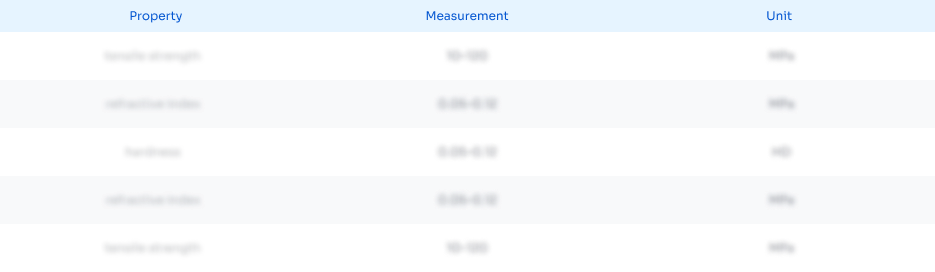
Abstract
Description
Claims
Application Information

- R&D Engineer
- R&D Manager
- IP Professional
- Industry Leading Data Capabilities
- Powerful AI technology
- Patent DNA Extraction
Browse by: Latest US Patents, China's latest patents, Technical Efficacy Thesaurus, Application Domain, Technology Topic, Popular Technical Reports.
© 2024 PatSnap. All rights reserved.Legal|Privacy policy|Modern Slavery Act Transparency Statement|Sitemap|About US| Contact US: help@patsnap.com