High-performance beryllium aluminum alloy and preparation method thereof
A high-performance technology of beryllium aluminum alloy, which is applied in the field of high specific strength and high corrosion resistance beryllium aluminum alloy and its preparation, can solve the problems of poor corrosion resistance of beryllium aluminum alloy, and achieve improved mechanical properties, enhanced strength and durability Corrosive, density-reducing effect
- Summary
- Abstract
- Description
- Claims
- Application Information
AI Technical Summary
Problems solved by technology
Method used
Examples
Embodiment 1
[0033] 1) Material preparation: first weigh the metal materials containing the following components and their contents by weight: Be: 40%, Ni: 4%, Mg4%, Ag: 0.5%, Si: 2%, Sr: 0.15%, Zr: 0.15 %, Cr: 0.15%, Sc: 0.2%, and the balance is Al and unavoidable impurities.
[0034] 2) Put the above-mentioned metal materials into a high-temperature melting furnace and heat them to melt them. The melting temperature is 750°C and the content of each component in the furnace is inspected and adjusted continuously to achieve the content range of each element mentioned above.
[0035] 3) Put silicon carbide, graphene and aluminum powder into a ball mill for ball milling, and then add the mixed powder after ball milling into the molten aluminum water by blowing it into the molten aluminum water with an air pressure of 0.2Mpa; and fully stir to make The mixed powder is mixed evenly in the furnace. Among them, the ball milling parameters are: the ball-to-material ratio is 5:1, the rotating spe...
Embodiment 2
[0045] 1) Material preparation: first weigh aluminum ingots containing the following components and their contents according to weight: Be: 50%, Ni: 3.5%, Mg4.5%, Ag: 0.1%, Si: 4.5%, Sr: 0.25%, Zr : 0.1%, Cr: 0.25%, Sc: 0.35%, the balance is Al and unavoidable impurities.
[0046] 2) Put the above-mentioned aluminum ingot into a high-temperature melting furnace and heat it to melt it. The melting temperature is 780°C and the content of each component in the furnace is checked and adjusted continuously to reach the content range of each element.
[0047] 3) Put silicon carbide, graphene and aluminum powder into a ball mill for ball milling, and then add the mixed powder after ball milling into the molten aluminum water by blowing it in with a nitrogen blowing machine, and the air pressure is 0.3Mpa; and fully stir to make The mixed powder is mixed evenly in the furnace. The ball milling parameters are as follows: the ball-to-material ratio is 5:1, the rotating speed is 350r / mi...
Embodiment 3
[0057] 1) Material preparation: first weigh aluminum ingots containing the following components and their contents according to weight: Be: 35%, Ni: 5%, Mg5%, Ag: 2%, Si: 0.2%, Sr: 0.1%, Zr: 0.35 %, Cr: 0.1%, Sc: 0.1%, and the balance is Al and unavoidable impurities.
[0058] 2) Put the above-mentioned aluminum ingot into a high-temperature melting furnace and heat it to melt it. The melting temperature is 780°C and the content of each component in the furnace is checked and adjusted continuously to reach the content range of each element.
[0059] 3) Put silicon carbide, graphene and aluminum powder into a ball mill for ball milling, and then add the mixed powder after ball milling into the molten aluminum water by blowing it in with a nitrogen blowing machine, and the air pressure is 0.3Mpa; and fully stir to make The mixed powder is mixed evenly in the furnace. The ball milling parameters are as follows: the ball-to-material ratio is 5:1, the rotating speed is 350r / min, a...
PUM
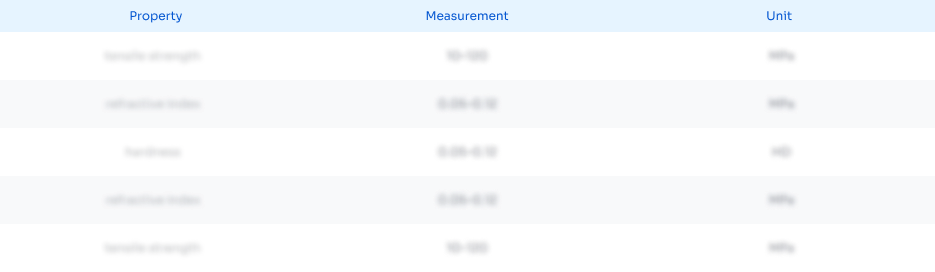
Abstract
Description
Claims
Application Information

- R&D Engineer
- R&D Manager
- IP Professional
- Industry Leading Data Capabilities
- Powerful AI technology
- Patent DNA Extraction
Browse by: Latest US Patents, China's latest patents, Technical Efficacy Thesaurus, Application Domain, Technology Topic, Popular Technical Reports.
© 2024 PatSnap. All rights reserved.Legal|Privacy policy|Modern Slavery Act Transparency Statement|Sitemap|About US| Contact US: help@patsnap.com