Process and system for improving operation period of vanadium pentoxide stripping and deamination tower,
A vanadium pentoxide, steam stripping and deamination technology, which is applied in the field of vanadium slag extraction wastewater treatment, can solve the problems affecting the continuous production and operation of vanadium pentoxide, non-continuous production of vanadium pentoxide, economic loss and environmental protection pressure, etc. To achieve the effect of improving the system operation cycle, ensuring the discharge of ammonia removal standards, and reasonable equipment structure
- Summary
- Abstract
- Description
- Claims
- Application Information
AI Technical Summary
Problems solved by technology
Method used
Image
Examples
Embodiment 1
[0030] As shown in the figure, the acidic ammonium salt pretreatment system for improving the operation cycle of the vanadium pentoxide stripping and deamination tower has a first-level silicon removal tank 1, a second-level silicon removal tank 3, a first-level chromium and calcium removal tank 5, and a second-level silicon removal tank 5. The first-level decalcification tank 7, the liquid outlet of the first-level desiliconization tank 1 is communicated with the second-level desiliconization tank 3 through a pipeline, and the acidic ammonium salt vanadium precipitation wastewater inlet of the first-level desiliconization tank 1 is provided with an acidic ammonium salt The vanadium precipitation wastewater pipeline, the acidic ammonium salt vanadium precipitation wastewater inlet pipeline of the first-level silicon removal tank is provided with a valve a; the pipeline between the first-level silicon removal tank 1 and the second-level silicon removal tank 3 is sequentially equi...
Embodiment 2
[0037] The acidic ammonium salt pretreatment system for increasing the operating cycle of the vanadium pentoxide stripping deamination tower is the same as in Example 1.
[0038] The operation process of the vanadium pentoxide stripping deamination tower to increase the operating cycle process system is as follows: before the process system is started, all valves are closed;
[0039] (1) Open the valve a, send the acidic ammonium salt vanadium precipitation wastewater (silicon 0.7g / L, calcium 0.4g / L, hexavalent chromium 1.3g / L) at a temperature of 70°C into the primary silicon removal tank 1, and close the valve a, start the stirring paddle, add lime powder (particle size: 400 mesh, active CaO content 64%), control the pH value to 10.5, react for 30 minutes, carry out silicon removal once, analyze and detect the silicon content of the first-level silicon removal tank solution 0.06g / L, start the filter press pump I9, and pass the primary silicon removal solution through the fi...
Embodiment 3
[0044] The acidic ammonium salt pretreatment system for increasing the operating cycle of the vanadium pentoxide stripping deamination tower is the same as in Example 1.
[0045] The operation process of the vanadium pentoxide stripping deamination tower to increase the operating cycle process system is as follows: before the process system is started, all valves are closed;
[0046] (1) Open the valve a, send the acidic ammonium salt vanadium precipitation wastewater (silicon 0.3g / L, calcium 0.1g / L, hexavalent chromium 1.6g / L) at a temperature of 60°C into the primary silicon removal tank 1, and close the valve a, start the stirring paddle, add lime powder (particle size 350 mesh, active CaO content 76%), control the pH value to 9.8, react for 25 minutes, perform a silicon removal, analyze and detect that the silicon content of the first-level silicon removal tank solution is 0.06g / L, start Filter press pump I9, which separates the primary silicon removal solution through fil...
PUM
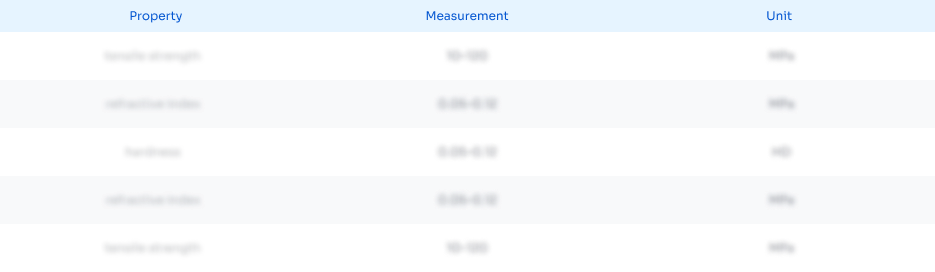
Abstract
Description
Claims
Application Information

- Generate Ideas
- Intellectual Property
- Life Sciences
- Materials
- Tech Scout
- Unparalleled Data Quality
- Higher Quality Content
- 60% Fewer Hallucinations
Browse by: Latest US Patents, China's latest patents, Technical Efficacy Thesaurus, Application Domain, Technology Topic, Popular Technical Reports.
© 2025 PatSnap. All rights reserved.Legal|Privacy policy|Modern Slavery Act Transparency Statement|Sitemap|About US| Contact US: help@patsnap.com