A continuous refining process of blister copper by fire method
A blister copper and pyrotechnic technology, applied in the field of non-ferrous metallurgy, can solve the problems of low utilization rate of casting equipment, long operation time, high labor intensity, etc., and achieve the goal of improving equipment utilization rate, shortening operation time and high automation level Effect
- Summary
- Abstract
- Description
- Claims
- Application Information
AI Technical Summary
Problems solved by technology
Method used
Image
Examples
Embodiment Construction
[0043] The technical solutions of the present invention will be further described below according to specific embodiments. The protection scope of the present invention is not limited to the following examples, which are listed for illustrative purposes only and do not limit the present invention in any way.
[0044] figure 1 It is a structural schematic diagram of the device used in the blister copper pyroprocess continuous refining process of an embodiment of the present invention, as figure 1 As shown, the blister copper continuous refining device includes a furnace body 1 and a flue port 6 arranged on the top of the furnace body 1. The furnace body 1 has a feeding oxidation zone 101, a reduction zone 102 and Casting area 103, carry out feeding melting, oxidation, reduction and casting process simultaneously, four cycles are carried out simultaneously in the same furnace, wherein reduction area 102 is located between feeding oxidation area 101 and casting area 103, so that...
PUM
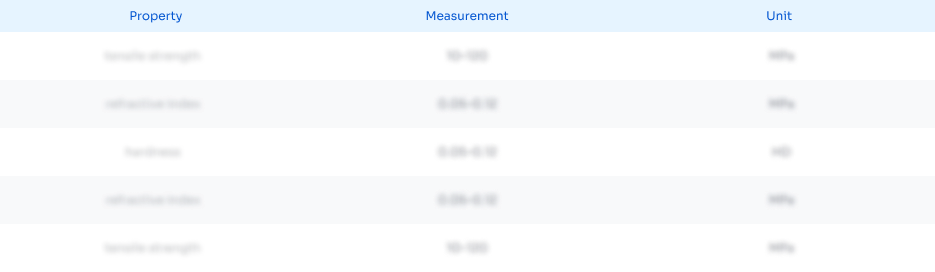
Abstract
Description
Claims
Application Information

- R&D
- Intellectual Property
- Life Sciences
- Materials
- Tech Scout
- Unparalleled Data Quality
- Higher Quality Content
- 60% Fewer Hallucinations
Browse by: Latest US Patents, China's latest patents, Technical Efficacy Thesaurus, Application Domain, Technology Topic, Popular Technical Reports.
© 2025 PatSnap. All rights reserved.Legal|Privacy policy|Modern Slavery Act Transparency Statement|Sitemap|About US| Contact US: help@patsnap.com