Anticorrosion sound-insulating glass fiber and preparation method thereof
A glass fiber and corrosion-resistant technology, applied in glass manufacturing equipment, glass molding, manufacturing tools, etc., can solve the problems of no sound insulation, heat insulation effect, single glass function, poor wear resistance, etc., and achieve good sound insulation effect , good sound insulation effect and low production cost
- Summary
- Abstract
- Description
- Claims
- Application Information
AI Technical Summary
Problems solved by technology
Method used
Examples
Embodiment 1
[0023] The glass fiber material with good corrosion resistance and sound insulation in this embodiment is made of the following raw materials in parts by weight: 50 parts of nano-silica, 3 parts of quartz sand, 2 parts of strontium carbonate, 5 parts of aluminum oxide, 4 parts of kaolin, sodium phosphate 2 parts, 1 part of potassium oxide, 1 part of barium oxide, 1 part of cobalt oxide, 1 part of manganese dioxide, 100 parts of absolute ethanol;
[0024] The preparation method of the good corrosion-resistant and sound-insulating glass fiber material of this embodiment comprises the following steps:
[0025] S1. Weighing each raw material according to parts by weight;
[0026] S2. Mix all the components into a ball mill for ball milling, mill for 13 hours, dry, pass through a 100-mesh sieve, heat up to 1100°C at a rate of 9°C / min, keep warm for 50min, and melt to form a uniform molten glass for later use;
[0027] S3. Rapidly pour the molten glass obtained in step S2 into a si...
Embodiment 2
[0032] The glass fiber material with good corrosion resistance and sound insulation in this embodiment is made of the following raw materials in parts by weight: 70 parts of nano-silica, 7 parts of quartz sand, 6.5 parts of strontium carbonate, 8.8 parts of aluminum oxide, 10 parts of kaolin, sodium phosphate 6 parts, 3 parts of potassium oxide, 3 parts of barium oxide, 3.6 parts of cobalt oxide, 3.6 parts of manganese dioxide, 150 parts of absolute ethanol;
[0033] The preparation method of the good corrosion-resistant and sound-insulating glass fiber material of this embodiment comprises the following steps:
[0034] S1. Weighing each raw material according to parts by weight;
[0035] S2. Mix the components into a ball mill for ball milling, mill for 16 hours, dry, pass through a 140-mesh sieve, heat up to 1150°C at a rate of 15°C / min, keep warm for 60min, and melt to form a uniform molten glass, which is ready for use;
[0036] S3. Rapidly pour the molten glass obtained ...
Embodiment 3
[0041] The glass fiber material with good corrosion resistance and sound insulation in this embodiment is made of the following raw materials in parts by weight: 40 parts of nano silicon dioxide, 5 parts of quartz sand, 5.5 parts of strontium carbonate, 6.8 parts of aluminum oxide, 7 parts of kaolin, sodium phosphate 4 parts, 2 parts of potassium oxide, 2 parts of barium oxide, 2.3 parts of cobalt oxide, 2.3 parts of manganese dioxide, 125 parts of absolute ethanol;
[0042] The preparation method of the good corrosion-resistant and sound-insulating glass fiber material of this embodiment comprises the following steps:
[0043] S1. Weighing each raw material according to parts by weight;
[0044] S2. Mix the components into a ball mill for ball milling, mill for 14.5 hours, dry, pass through a 120-mesh sieve, heat up to 1130°C at a rate of 12°C / min, keep warm for 55min, and melt to form a uniform glass liquid, which is ready for use;
[0045]S3. Quickly pour the molten glass ...
PUM
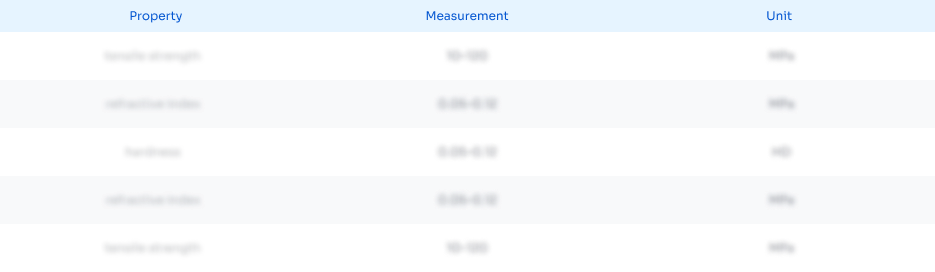
Abstract
Description
Claims
Application Information

- Generate Ideas
- Intellectual Property
- Life Sciences
- Materials
- Tech Scout
- Unparalleled Data Quality
- Higher Quality Content
- 60% Fewer Hallucinations
Browse by: Latest US Patents, China's latest patents, Technical Efficacy Thesaurus, Application Domain, Technology Topic, Popular Technical Reports.
© 2025 PatSnap. All rights reserved.Legal|Privacy policy|Modern Slavery Act Transparency Statement|Sitemap|About US| Contact US: help@patsnap.com