Preparation method of high-glossiness wear-resistant impregnated paper
A wear-resistant and impregnated paper technology, applied in paper, papermaking, textiles and papermaking, etc., can solve the problems of not meeting the requirements of the paper market, low gloss, poor wear resistance, etc., to improve interface compatibility and gloss Degree, improve the effect of wear resistance
- Summary
- Abstract
- Description
- Claims
- Application Information
AI Technical Summary
Problems solved by technology
Method used
Examples
example 1
[0023]Weigh and grind 32g of alumina for 11min to obtain alumina powder, then mix alumina powder, polyethylene glycol and deionized water in a mass ratio of 3:1:6 and place them in a beaker and stir for 16min to obtain an alumina aqueous dispersion , according to the volume ratio of 5:2:1, the aluminum oxide aqueous dispersion, deionized water and absolute ethanol were mixed and placed in a four-necked flask equipped with a condenser, a thermometer and a stirrer, at a temperature of 70 ° C Stir and reflux for 27 minutes to obtain a reflux suspension; add xylene formaldehyde resin with 3% of the mass of the reflux suspension and carbon black with 1% of the mass of the reflux suspension to the reflux suspension, continue to insulate and stir for 45 minutes, and pour it into a suction filter after stirring. Filter for 10 minutes to obtain the filter residue, wash the filter residue with deionized water for 3 times, and finally put the washed filter residue in an oven, dry it at 72...
example 2
[0025] Weigh 34g of alumina and grind it for 12min to obtain alumina powder, then mix alumina powder, polyethylene glycol and deionized water in a mass ratio of 3:1:6, put them in a beaker and stir for 18min to obtain an alumina aqueous dispersion , according to the volume ratio of 5:2:1, the aluminum oxide aqueous dispersion, deionized water and absolute ethanol were mixed and placed in a four-necked flask equipped with a condenser, a thermometer and a stirrer, at a temperature of 75 ° C Stir and reflux for 29 minutes to obtain a reflux suspension; add 3% xylene formaldehyde resin and 1% carbon black of the reflux suspension quality to the reflux suspension, continue to insulate and stir for 50 minutes, and pour it into a suction filter after stirring. Filter for 11 minutes to obtain the filter residue, wash the filter residue 4 times with deionized water, and finally put the washed filter residue in an oven, dry it at 73°C for 1.5 hours, cool naturally to room temperature, gr...
example 3
[0027] Weigh 36g of alumina and grind it for 13 minutes to obtain alumina powder, then mix alumina powder, polyethylene glycol and deionized water in a mass ratio of 3:1:6, put them in a beaker and stir for 20 minutes to obtain an alumina aqueous dispersion , according to the volume ratio of 5:2:1, the aluminum oxide aqueous dispersion, deionized water and absolute ethanol were mixed and placed in a four-necked flask equipped with a condenser, a thermometer and a stirrer, at a temperature of 80 ° C Stir and reflux for 32 minutes to obtain a reflux suspension; add xylene formaldehyde resin with 3% of the mass of the reflux suspension and carbon black with 1% of the mass of the reflux suspension to the reflux suspension, continue to insulate and stir for 60 minutes, and pour it into a suction filter after stirring. Filter for 12 minutes to obtain the filter residue, wash the filter residue 5 times with deionized water, and finally put the washed filter residue in an oven, dry at ...
PUM
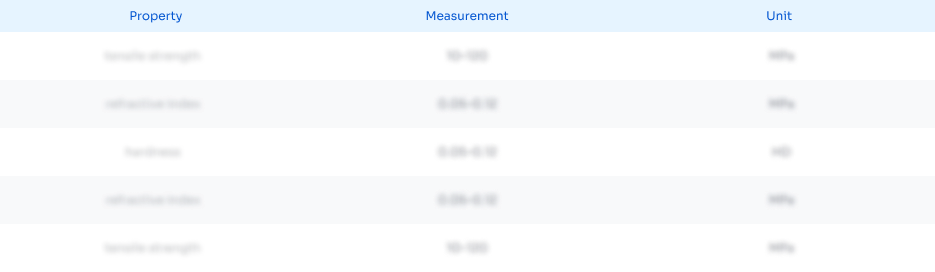
Abstract
Description
Claims
Application Information

- R&D
- Intellectual Property
- Life Sciences
- Materials
- Tech Scout
- Unparalleled Data Quality
- Higher Quality Content
- 60% Fewer Hallucinations
Browse by: Latest US Patents, China's latest patents, Technical Efficacy Thesaurus, Application Domain, Technology Topic, Popular Technical Reports.
© 2025 PatSnap. All rights reserved.Legal|Privacy policy|Modern Slavery Act Transparency Statement|Sitemap|About US| Contact US: help@patsnap.com