Surface treatment method of wood female mold body of electric arc spraying mold
A technology of arc spraying and surface treatment, which is applied in the direction of surface coating liquid devices, coatings, epoxy resin coatings, etc., which can solve the problems of difficult removal of metal shells, destructive demoulding, and time-consuming, etc. Achieve the effects of saving demoulding time, small surface damage and improving production efficiency
- Summary
- Abstract
- Description
- Claims
- Application Information
AI Technical Summary
Problems solved by technology
Method used
Examples
Embodiment 1
[0031] 1) Grinding off the burrs on the surface of the master mold, and disposing of debris on the surface;
[0032] 2) Prepare epoxy resin glue solution at 23°C, the epoxy glue solution is calculated by weight ratio, and the proportion is epoxy resin E51: A50 modified amine curing agent: epoxy diluent HK-66 = 100:40: 10;
[0033] 3) Spray a layer of prepared epoxy resin glue on the surface of the master mold, heat it at 120°C for 3 minutes, take it out and cool it to room temperature;
[0034] 4) Repeat step 3) twice;
[0035] 5) Spray the emulsified simethicone release agent evenly on the surface of the mold, and heat it at 100°C for 15 minutes, then take out the mold and cool it down to room temperature;
[0036] 6) Spray a layer of polyurethane resin on the surface after spraying the release agent, and dry it for 15 minutes at a temperature of 25°C and a humidity of 75%;
[0037] 7) After the polyurethane resin is dry, the surface treatment of the entire wooden master m...
Embodiment 2
[0039] 1) Grinding off the burrs on the surface of the master mold, and disposing of debris on the surface;
[0040] 2) Prepare epoxy resin glue solution at 23°C, the epoxy glue solution is calculated by weight ratio, and the proportion is epoxy resin E51: A50 modified amine curing agent: epoxy diluent HK-66 = 100:40: 10;
[0041] 3) Spray a layer of prepared epoxy resin glue on the surface of the master mold, and harden at 25°C for not less than 8 hours;
[0042] 4) Repeat step 3) twice;
[0043] 5) Spray the emulsified simethicone release agent evenly on the surface of the mold, and dry it at 25°C for 30 minutes;
[0044] 6) Spray a layer of polyurethane resin on the surface after spraying the release agent, and dry it for 15 minutes at a temperature of 25°C and a humidity of 75%;
[0045] 7) After the polyurethane resin is dry, the surface treatment of the entire wooden master mold for electric arc spraying is completed.
Embodiment 3
[0047] 1) Grinding off the burrs on the surface of the master mold, and disposing of debris on the surface;
[0048] 2) Prepare epoxy resin glue solution at 23°C, the epoxy glue solution is calculated by weight ratio, and the proportion is epoxy resin E51: A50 modified amine curing agent: epoxy diluent HK-66 = 100:40: 10;
[0049] 3) Spray a layer of prepared epoxy resin glue on the surface of the master mold, heat it at 90°C for 15 minutes, take it out and cool it to room temperature;
[0050] 4) Repeat step 3) twice;
[0051] 5) Spray the emulsified simethicone release agent evenly on the surface of the mold, heat at 100°C for 15 minutes and cool to room temperature;
[0052] 6) Spray a layer of polyurethane resin on the surface after spraying the release agent, and dry it for 15 minutes at a temperature of 25°C and a humidity of 75%;
[0053] 7) After the polyurethane resin is dry, the surface treatment of the entire wooden master mold for electric arc spraying is complete...
PUM
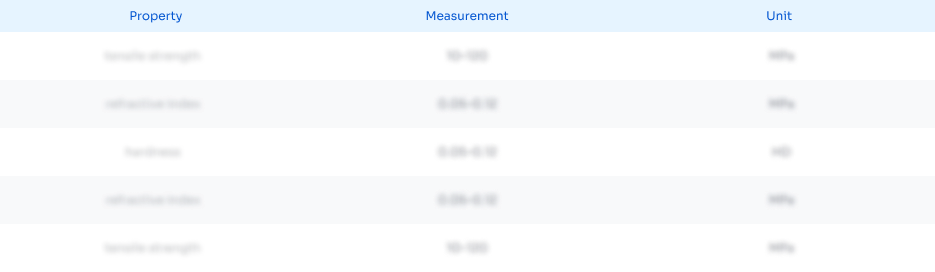
Abstract
Description
Claims
Application Information

- R&D
- Intellectual Property
- Life Sciences
- Materials
- Tech Scout
- Unparalleled Data Quality
- Higher Quality Content
- 60% Fewer Hallucinations
Browse by: Latest US Patents, China's latest patents, Technical Efficacy Thesaurus, Application Domain, Technology Topic, Popular Technical Reports.
© 2025 PatSnap. All rights reserved.Legal|Privacy policy|Modern Slavery Act Transparency Statement|Sitemap|About US| Contact US: help@patsnap.com