Optical reflectivity surface treatment method
A surface treatment, optical reflection technology, applied in the direction of anodizing, can solve the problems of poor wear resistance, poor light resistance, easy conductivity, etc., to improve wear and corrosion resistance, strong selective absorption and scattering effects Effect
- Summary
- Abstract
- Description
- Claims
- Application Information
AI Technical Summary
Problems solved by technology
Method used
Image
Examples
Embodiment Construction
[0023] In order to have a clearer understanding of the technical features, purposes and effects of the present invention, the specific implementation manners of the present invention will now be described with reference to the accompanying drawings.
[0024] The optical reflectivity surface treatment method of the present invention has greatly improved the surface performance of the product, especially in the optical reflectivity, can greatly reduce the reflectivity, so that the product surface can meet the assembly requirements of optical devices, and will be due to Light reflected from the housing has minimal impact on the optics.
[0025] A kind of optical reflectivity surface treatment method of the present invention, in its preferred embodiment, please refer to figure 1 Shown, be the flow chart diagram of preferred embodiment of the present invention, this method comprises the following steps to the processing of product:
[0026] S101 After placing the product on the pr...
PUM
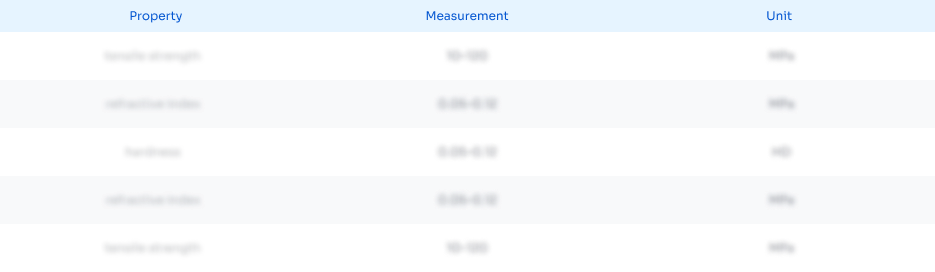
Abstract
Description
Claims
Application Information

- R&D Engineer
- R&D Manager
- IP Professional
- Industry Leading Data Capabilities
- Powerful AI technology
- Patent DNA Extraction
Browse by: Latest US Patents, China's latest patents, Technical Efficacy Thesaurus, Application Domain, Technology Topic, Popular Technical Reports.
© 2024 PatSnap. All rights reserved.Legal|Privacy policy|Modern Slavery Act Transparency Statement|Sitemap|About US| Contact US: help@patsnap.com