Hot-galvanized aluminum-magnesium alloy steel plate and production process thereof
An aluminum-magnesium alloy and production process technology, which is applied in hot-dip plating process, metal material coating process, coating and other directions, can solve the problems of backward production technology of hot-dip galvanized aluminum-magnesium alloy steel plate, etc. Corrosion resistance and high control accuracy
- Summary
- Abstract
- Description
- Claims
- Application Information
AI Technical Summary
Problems solved by technology
Method used
Examples
Embodiment 1
[0048] A production process of hot-dip galvanized aluminum-magnesium alloy steel plate, comprising the following steps:
[0049] Put the zinc ingot into the zinc pot for heating and melting;
[0050] Put magnesium-zinc alloy ingots, aluminum-zinc alloy ingots and rare earths, the rare earths include cerium rare earths and lanthanum rare earths, take samples after melting, perform spectral analysis on the samples, measure each chemical composition, and then conduct zinc ingots, Continue to add magnesium-zinc alloy ingots, aluminum-zinc alloy ingots and rare earth, stir evenly, and then perform spectral analysis of the sample until the content requirements of the following components are met:
[0051] Aluminum: 0.22%;
[0052] Magnesium: 0.55%;
[0053] Cerium: 0.025%;
[0054] Lanthanum: 0.025%;
[0055] Antimony: <0.02%;
[0056] Zinc: the rest;
[0057] Smooth the steel plate, and then carry out chromic acid passivation treatment on the front;
[0058] Galvanizing the ...
Embodiment 2
[0060] A production process of hot-dip galvanized aluminum-magnesium alloy steel plate, comprising the following steps:
[0061] Put the zinc ingot into the zinc pot for heating and melting;
[0062] Put magnesium-zinc alloy ingots, aluminum-zinc alloy ingots and rare earths, the rare earths include cerium rare earths and lanthanum rare earths, take samples after melting, perform spectral analysis on the samples, measure each chemical composition, and then conduct zinc ingots, Continue to add magnesium-zinc alloy ingots, aluminum-zinc alloy ingots and rare earth, stir evenly, and then perform spectral analysis of the sample until the content requirements of the following components are met:
[0063] Aluminum: 0.2%;
[0064] Magnesium: 0.5%;
[0065] Cerium: 0.02%;
[0066] Lanthanum: 0.02%;
[0067] Antimony: <0.02%;
[0068] Zinc: the rest;
[0069] Smooth the steel plate, and then carry out chromic acid passivation treatment on the front;
[0070] Galvanizing the stee...
Embodiment 3
[0072] A production process of hot-dip galvanized aluminum-magnesium alloy steel plate, comprising the following steps:
[0073] Put the zinc ingot into the zinc pot for heating and melting;
[0074]Put magnesium-zinc alloy ingots, aluminum-zinc alloy ingots and rare earths, the rare earths include cerium rare earths and lanthanum rare earths, take samples after melting, perform spectral analysis on the samples, measure each chemical composition, and then conduct zinc ingots, Continue to add magnesium-zinc alloy ingots, aluminum-zinc alloy ingots and rare earth, stir evenly, and then perform spectral analysis of the sample until the content requirements of the following components are met:
[0075] Aluminum: 0.25%;
[0076] Magnesium: 0.6%;
[0077] Cerium: 0.03%;
[0078] Lanthanum: 0.03%;
[0079] Antimony: <0.02%;
[0080] Zinc: the rest;
[0081] Smooth the steel plate, and then carry out chromic acid passivation treatment on the front;
[0082] Galvanizing the stee...
PUM
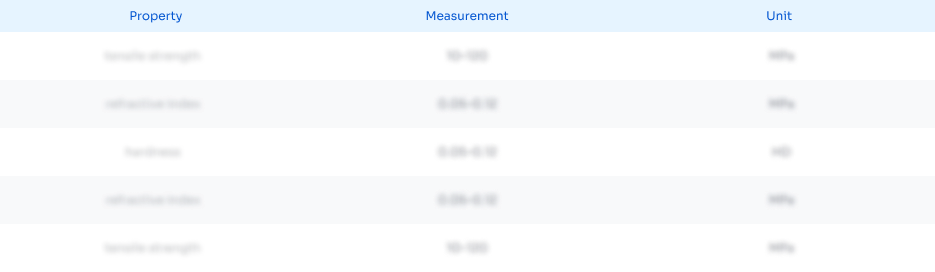
Abstract
Description
Claims
Application Information

- R&D
- Intellectual Property
- Life Sciences
- Materials
- Tech Scout
- Unparalleled Data Quality
- Higher Quality Content
- 60% Fewer Hallucinations
Browse by: Latest US Patents, China's latest patents, Technical Efficacy Thesaurus, Application Domain, Technology Topic, Popular Technical Reports.
© 2025 PatSnap. All rights reserved.Legal|Privacy policy|Modern Slavery Act Transparency Statement|Sitemap|About US| Contact US: help@patsnap.com