A kind of process method of continuous casting and rolling
A process method, continuous casting and rolling technology, applied in the direction of manufacturing tools, metal rolling, metal rolling, etc., can solve the problems of energy consumption, long heating time, affecting the thickness of the final product, achieve uniform thickness, eliminate scale , Improve the effect of warping skin defects
- Summary
- Abstract
- Description
- Claims
- Application Information
AI Technical Summary
Problems solved by technology
Method used
Image
Examples
Embodiment Construction
[0029] The preferred embodiments of the present invention will be described in detail below with reference to the accompanying drawings.
[0030] Such as Figure 4 Shown, the technological method of continuous casting and rolling among the present invention, comprises successively continuous casting-rough rolling-induction heating-finish rolling-laminar cooling-flying shear-curling finished product step; This technological method is especially in continuous casting and rough rolling Mechanical cleaning is carried out between the steps. The mechanical cleaning here is to use the burner to heat the iron oxide skin layer and other defects with a thickness of 1mm to 5mm on the surface of the slab to a molten state, and then use 1.5MP to 5MP water to melt the oxides in the molten state. clear.
[0031] Specifically, the burner is used to heat the surface of the slab, so that the surface temperature of the slab can rise to above 1500°C and the surface of the slab is in a molten sta...
PUM
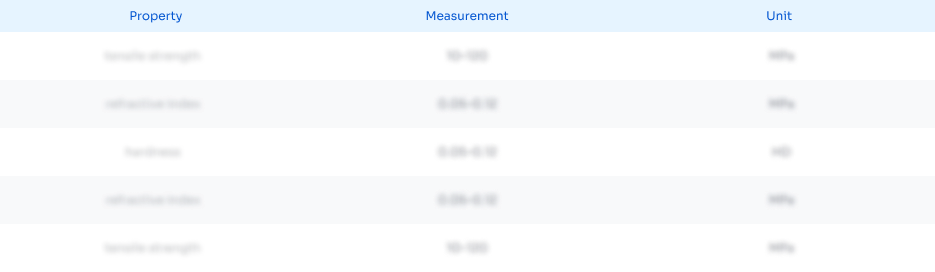
Abstract
Description
Claims
Application Information

- R&D Engineer
- R&D Manager
- IP Professional
- Industry Leading Data Capabilities
- Powerful AI technology
- Patent DNA Extraction
Browse by: Latest US Patents, China's latest patents, Technical Efficacy Thesaurus, Application Domain, Technology Topic, Popular Technical Reports.
© 2024 PatSnap. All rights reserved.Legal|Privacy policy|Modern Slavery Act Transparency Statement|Sitemap|About US| Contact US: help@patsnap.com