Method for preparing oxygen reduction catalyst from cobalt sulfide
A technology of sulfide and catalyst, which is applied in the field of preparation of cobalt sulfide to prepare oxygen reduction catalyst, can solve the problems such as cost and scarcity hindering wide implementation, poor methanol resistance, poor stability, etc., and achieve high product quality and good stability. good performance
- Summary
- Abstract
- Description
- Claims
- Application Information
AI Technical Summary
Problems solved by technology
Method used
Image
Examples
preparation example Construction
[0019] A method for preparing an oxygen reduction catalyst from a cobalt sulfide of the present invention, especially for preparing an oxygen reduction catalyst from a cobalt sulfide derived from a cobalt-based metal organic framework, the preparation process includes the following steps:
[0020] 1) Cobalt nitrate hexahydrate (52.4 mg, 0.2 mmol) and 4,4'-bpdc (48.4 mg, 0.2 mmol) were dissolved in 23 mL of DMF. 1,3-bib (31.5 mg, 0.15 mmol) was dissolved in 2 mL DMF respectively.
[0021] 2) After the samples obtained in step 1 were ultrasonically treated for 1 minute, the solutions were mixed, transferred to a reaction kettle (50cm3), and heated at 1.2°C min -1 The heating rate was heated to 120°C; kept at 120°C for 48 hours, then slowly cooled to room temperature (0.4°C min -1 ); after cooling to room temperature, the purple crystals were separated by decanting the mother liquor and washed with DMF, and then dried to obtain a cobalt-based metal-organic framework.
[0022] 3...
Embodiment 1
[0026] Cobalt nitrate hexahydrate (52.4 mg, 0.2 mmol) and 4,4'-bpdc (48.4 mg, 0.2 mmol) were dissolved in 23 mL of DMF. 1,3-Bis(imidazol-1-yl)benzene (1,3-bib) (31.5 mg, 0.15 mmol) was dissolved in 2 mL of DMF respectively. After sonication for 1 min, the solutions were mixed, transferred to a reaction kettle (50 cm3), and heated at 1.2 °C min -1 The heating rate is heated to 120 °C. Keep at 120°C for 48 hours, then slowly cool to room temperature (0.4°C min -1 ). After cooling to room temperature, the purple crystals were separated by decanting the mother liquor and washed with DMF, and then dried to obtain a cobalt-based metal-organic framework.
[0027] The prepared crystals (2.0 g) were weighed into a ceramic vessel and transferred to the outlet port of the tube furnace. Thioacetamide (1.0 g) was weighed into a ceramic vessel and transferred to the inlet port of the tube furnace. Pyrolysis at 700°C for 2 hours under nitrogen with a heating rate of 5°C min -1 , to obt...
Embodiment 2
[0031] Cobalt nitrate hexahydrate (52.4 mg, 0.2 mmol) and 4,4'-bpdc (48.4 mg, 0.2 mmol) were dissolved in 23 mL of DMF. 1,3-Bis(imidazol-1-yl)benzene (1,3-bib) (31.5 mg, 0.15 mmol) was dissolved in 2 mL of DMF respectively. After sonication for 1 min, the solutions were mixed, transferred to a reaction kettle (50 cm3), and heated at 1.2 °C min -1 Heating rate Heat up to 120°C. Keep at 120°C for 48 hours, then slowly cool to room temperature (0.4°C min -1 ). After cooling to room temperature, the purple crystals were separated by decanting the mother liquor and washed with DMF, and then dried to obtain a cobalt-based metal-organic framework.
[0032] The prepared crystals (2.0 g) were weighed into a ceramic vessel and transferred to the outlet port of the tube furnace. Thioacetamide (1.0 g) was weighed into a ceramic vessel and transferred to the inlet port of the tube furnace. Pyrolysis at 600°C for 2 hours under nitrogen with a heating rate of 5°C min -1 , to obtain nit...
PUM
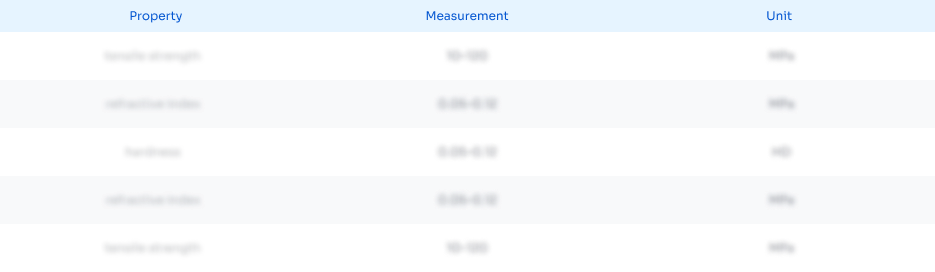
Abstract
Description
Claims
Application Information

- R&D
- Intellectual Property
- Life Sciences
- Materials
- Tech Scout
- Unparalleled Data Quality
- Higher Quality Content
- 60% Fewer Hallucinations
Browse by: Latest US Patents, China's latest patents, Technical Efficacy Thesaurus, Application Domain, Technology Topic, Popular Technical Reports.
© 2025 PatSnap. All rights reserved.Legal|Privacy policy|Modern Slavery Act Transparency Statement|Sitemap|About US| Contact US: help@patsnap.com