Anti-corrosive coating for cement concrete crash-resisting wall and preparation method of anti-corrosive coating
A technology of cement concrete and anti-corrosion coatings, applied in the field of coatings, can solve problems such as performance that cannot meet market demand, and achieve the effects of not easy peeling off, guaranteed service life, and improved corrosion resistance
- Summary
- Abstract
- Description
- Claims
- Application Information
AI Technical Summary
Problems solved by technology
Method used
Image
Examples
Embodiment 1
[0025] An anti-corrosion coating for cement concrete anti-collision walls, comprising the following raw materials in parts by weight: 85 parts of hydroxyacrylic resin, 140 parts of epoxy resin, 4 parts of polyoxyethylene lauryl ether, 18 parts of mullite, polyoxypropylene glycerin 1 part of ether, 9 parts of polyimide, 2 parts of polymethylphenylsiloxane, 15 parts of thickener, 2 parts of vinyl bis stearamide, 3 parts of ethoxylated fatty alkylamine, silane 5 parts of coupling agent, 21 parts of propylene glycol methyl ether, 5 parts of calcium aluminum borosilicate.
[0026] Wherein, the thickener is formed by mixing sodium bentonite and cellulose ether in a weight ratio of 2:1.
[0027] In the present embodiment, the preparation method of the anti-corrosion coating for the cement concrete anti-collision wall, the steps are as follows:
[0028] 1) take mullite, pulverize, cross 60 mesh sieves, obtain mullite powder;
[0029] 2) Put the mullite powder into a calciner, calcin...
Embodiment 2
[0036] An anti-corrosion coating for cement concrete anti-collision walls, comprising the following raw materials in parts by weight: 86 parts of hydroxyacrylic resin, 143 parts of epoxy resin, 7 parts of polyoxyethylene lauryl ether, 21 parts of mullite, polyoxypropylene glycerin 1.5 parts of ether, 10 parts of polyimide, 3 parts of polymethylphenylsiloxane, 18 parts of thickener, 4 parts of vinyl bis stearamide, 5 parts of ethoxylated fatty alkylamine, silane 6 parts of coupling agent, 22 parts of propylene glycol methyl ether, 8 parts of calcium aluminum borosilicate.
[0037] Wherein, the thickener is formed by mixing sodium bentonite and cellulose ether in a weight ratio of 2:1.
[0038] In the present embodiment, the preparation method of the anti-corrosion coating for the cement concrete anti-collision wall, the steps are as follows:
[0039] 1) take mullite, pulverize, cross 70 mesh sieves, obtain mullite powder;
[0040] 2) Put the mullite powder into the calciner, ...
Embodiment 3
[0047] An anti-corrosion coating for cement concrete anti-collision walls, comprising the following raw materials in parts by weight: 87 parts of hydroxyacrylic resin, 145 parts of epoxy resin, 6 parts of polyoxyethylene lauryl ether, 20 parts of mullite, polyoxypropylene glycerin 2 parts of ether, 11 parts of polyimide, 3.5 parts of polymethylphenylsiloxane, 17 parts of thickener, 3 parts of vinyl bis stearamide, 4.5 parts of ethoxylated fatty alkylamine, silane 7 parts of coupling agent, 23 parts of propylene glycol methyl ether, 7 parts of calcium aluminum borosilicate.
[0048] Wherein, the thickener is formed by mixing sodium bentonite and cellulose ether in a weight ratio of 2:1.
[0049] In the present embodiment, the preparation method of the anti-corrosion coating for the cement concrete anti-collision wall, the steps are as follows:
[0050] 1) take mullite, pulverize, cross 70 mesh sieves, obtain mullite powder;
[0051] 2) Put the mullite powder into the calciner, ...
PUM
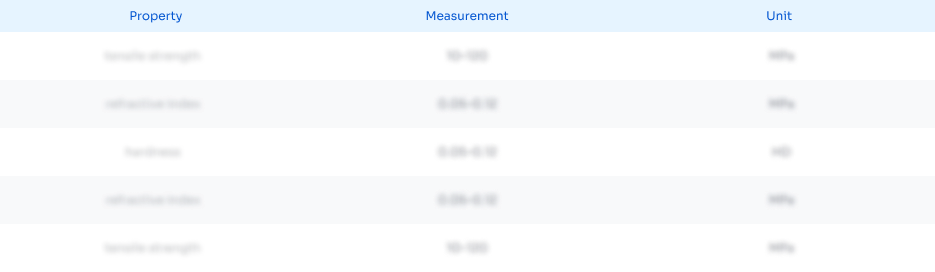
Abstract
Description
Claims
Application Information

- Generate Ideas
- Intellectual Property
- Life Sciences
- Materials
- Tech Scout
- Unparalleled Data Quality
- Higher Quality Content
- 60% Fewer Hallucinations
Browse by: Latest US Patents, China's latest patents, Technical Efficacy Thesaurus, Application Domain, Technology Topic, Popular Technical Reports.
© 2025 PatSnap. All rights reserved.Legal|Privacy policy|Modern Slavery Act Transparency Statement|Sitemap|About US| Contact US: help@patsnap.com