Blade-repairing type repair method of engine blade
An engine blade and repair method technology, applied in the directions of aircraft parts, transportation and packaging, can solve the problems of complex process and high cost, and achieve the effects of improving repair quality, improving accuracy and reducing cost
- Summary
- Abstract
- Description
- Claims
- Application Information
AI Technical Summary
Problems solved by technology
Method used
Image
Examples
Embodiment 1
[0044] If the leading edge corners of multiple blades of an integral blisk are damaged, a unified cutting position including the largest damage is selected, and after the damage is cut along the straight line from the blade tip to the leading edge, the patch design is performed to form a single-sided groove. According to the profile processing welding tool, the profile tolerance is processed according to -0.3mm, the blade and patch are assembled on the welding tool, and the arc welding method is used for welding. Use the welding robot to teach the welding trajectory, followed by repair welding. The tooling is removed after welding, and there is a small gap between the patch and the tooling, which is equivalent to the amount of pre-deformation. X-ray inspection was carried out on the repair welding, and no defects such as pores were found.
Embodiment 2
[0046] The trailing edge of a certain blade was damaged due to processing errors. After the damage was cut along the straight line from the tip to the trailing edge, a patch design was carried out. The curvature of the cut surface was large, and the arc-shaped plate was used to reduce the welding thickness. The welding tooling is processed according to the surface tolerance -0.2mm. After the blades and patches are assembled on the welding tooling, the welding robot is used to teach the welding trajectory, and the welding is performed with uniform welding parameters.
PUM
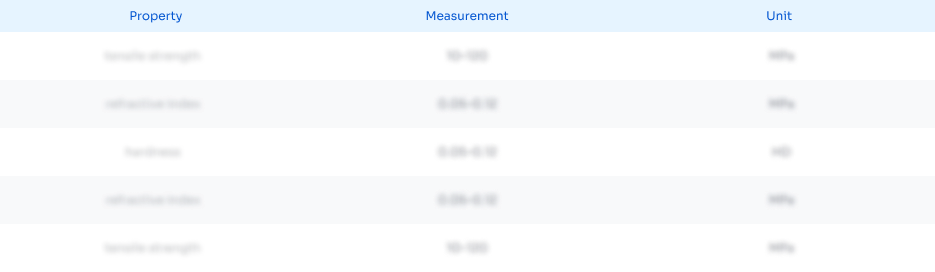
Abstract
Description
Claims
Application Information

- Generate Ideas
- Intellectual Property
- Life Sciences
- Materials
- Tech Scout
- Unparalleled Data Quality
- Higher Quality Content
- 60% Fewer Hallucinations
Browse by: Latest US Patents, China's latest patents, Technical Efficacy Thesaurus, Application Domain, Technology Topic, Popular Technical Reports.
© 2025 PatSnap. All rights reserved.Legal|Privacy policy|Modern Slavery Act Transparency Statement|Sitemap|About US| Contact US: help@patsnap.com