Manufacturing method of low-oxygen low-inclusion bearing steel
A technology for bearing steel and impurities, applied in the direction of manufacturing converters, etc., can solve the problems of uneven distribution of non-metallic inclusions, and the difficulty of steel performance to meet strict standard requirements.
- Summary
- Abstract
- Description
- Claims
- Application Information
AI Technical Summary
Problems solved by technology
Method used
Image
Examples
Embodiment 1
[0055]A method for preparing low-oxygen and low-inclusion bearing steel, including raw material preparation, converter smelting and alloying, LF+VD refining, continuous casting, rolling, slow cooling; controlling the chemical composition mass percentage of the bearing steel to be C 1.06, Si 0.7, Mn 1.30, Mo0.02, Ni 0.06, Cr 1.85, Co 0.02, V 0.02, Al S 0.01, Hf 0.02, Ta 0.01, Te 0.005, Cu0.05, S≤0.025, P≤0.025, [O]≤10×10 -6 , [H]≤2×10 -6 , the remainder being Fe and unavoidable impurities; The specific production steps are as follows:
[0056] (1) Raw material preparation
[0057] The converter with a capacity of 300t is used as the standard raw material, among which molten iron with P≤0.07%, S≤0.02% accounts for 87~88%, and scrap steel with P≤0.07%, S≤0.02%, Ti≤0.05% accounts for 8-10% %, the rest is iron lumps with P≤0.07%, S≤0.02%;
[0058] (2) Converter smelting
[0059] Converter smelting is used, the end point phosphorus is ≤0.01%, the end point carbon is ≥0.25%, th...
Embodiment 2
[0071] A method for preparing low-oxygen and low-inclusion bearing steel, including raw material preparation, converter smelting and alloying, LF+VD refining, continuous casting, rolling, and slow cooling; the chemical composition mass percentage content of the controlled bearing steel is C 1.08, Si 0.72, Mn 1.32, Mo0.04, Ni 0.07, Cr 1.88, Co 0.03, V 0.025, Al S 0.02, Hf 0.025, Ta 0.018, Te 0.006, Cu0.8, S≤0.025, P≤0.025, [O]≤10×10 -6 , [H]≤2×10 -6 , the remainder being Fe and unavoidable impurities; The specific production steps are as follows:
[0072] (1) Raw material preparation
[0073] The converter with a capacity of 300t is used as the standard raw material, among which molten iron with P≤0.07%, S≤0.02% accounts for 87~88%, and scrap steel with P≤0.07%, S≤0.02%, Ti≤0.05% accounts for 8-10% %, the rest is iron lumps with P≤0.07%, S≤0.02%;
[0074] (2) Converter smelting
[0075] Converter smelting is used, the end point phosphorus is ≤0.01%, the end point carbon i...
Embodiment 3
[0087] A method for preparing low-oxygen and low-inclusion bearing steel, including raw material preparation, converter smelting and alloying, LF+VD refining, continuous casting, rolling, slow cooling; controlling the chemical composition mass percentage of bearing steel to be C 1.1, Si0 .75, Mn 1.35, Mo0.05, Ni 0.08, Cr 1.9, Co 0.04, V 0.03, Al S 0.03, Hf 0.03, Ta 0.02, Te 0.008, Cu 0.1, S≤0.025, P≤0.025, [O]≤10×10 -6 , [H]≤2×10 -6 , the remainder being Fe and unavoidable impurities; The specific production steps are as follows:
[0088] (1) Raw material preparation
[0089] The converter with a capacity of 300t is used as the standard raw material, among which molten iron with P≤0.07%, S≤0.02% accounts for 87~88%, and scrap steel with P≤0.07%, S≤0.02%, Ti≤0.05% accounts for 8-10% %, the rest is iron lumps with P≤0.07%, S≤0.02%;
[0090] (2) Converter smelting
[0091] Converter smelting is used, the end point phosphorus is ≤0.01%, the end point carbon is ≥0.25%, the temp...
PUM
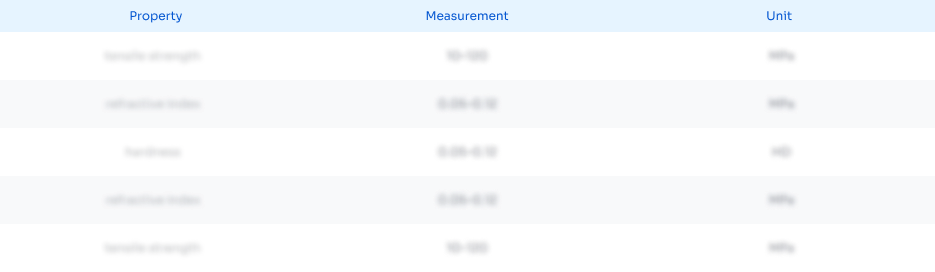
Abstract
Description
Claims
Application Information

- R&D
- Intellectual Property
- Life Sciences
- Materials
- Tech Scout
- Unparalleled Data Quality
- Higher Quality Content
- 60% Fewer Hallucinations
Browse by: Latest US Patents, China's latest patents, Technical Efficacy Thesaurus, Application Domain, Technology Topic, Popular Technical Reports.
© 2025 PatSnap. All rights reserved.Legal|Privacy policy|Modern Slavery Act Transparency Statement|Sitemap|About US| Contact US: help@patsnap.com