Control device and technology for corner cracks of microalloy steel sheet billet
A technology of micro-alloy steel and control equipment, which is applied in the field of thin slab continuous casting and rolling of steel, can solve the problems of reducing micro-alloy and nitrogen content, difficulty in stable control, and high difficulty, so as to reduce stress, increase cooling speed, and improve Effects on Tissue Plasticity
- Summary
- Abstract
- Description
- Claims
- Application Information
AI Technical Summary
Problems solved by technology
Method used
Image
Examples
Embodiment Construction
[0038] The specific implementation manners of the present invention will be further described in detail below in conjunction with the accompanying drawings and embodiments. The following examples are used to illustrate the present invention, but are not intended to limit the scope of the present invention.
[0039] An embodiment of a SS400-B steel thin slab with a mold thickness of 90 mm produced by a CSP at a continuous casting speed of 4.0 m / min will be further described below in conjunction with the accompanying drawings.
[0040] The micro-alloy steel thin slab corner crack control equipment in this embodiment includes a secondary cooling water distribution system, a crystallizer, and a newly enhanced spray system in the foot roll area of the narrow surface of the crystallizer. Among them, the secondary cooling water distribution system for the wide face of the slab adopts the original secondary cooling water distribution system based on target surface temperature contro...
PUM
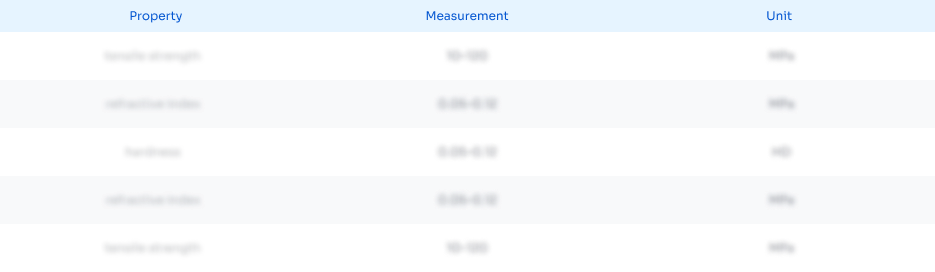
Abstract
Description
Claims
Application Information

- R&D
- Intellectual Property
- Life Sciences
- Materials
- Tech Scout
- Unparalleled Data Quality
- Higher Quality Content
- 60% Fewer Hallucinations
Browse by: Latest US Patents, China's latest patents, Technical Efficacy Thesaurus, Application Domain, Technology Topic, Popular Technical Reports.
© 2025 PatSnap. All rights reserved.Legal|Privacy policy|Modern Slavery Act Transparency Statement|Sitemap|About US| Contact US: help@patsnap.com