A post-converter decarburization process
A process method and decarburization technology, which is applied in the field of iron and steel smelting, can solve the problems of molten steel overoxidation, high cost, and reduced converter lining life, and achieve the effects of reducing oxide inclusions, simplifying the smelting process, and reducing production costs
- Summary
- Abstract
- Description
- Claims
- Application Information
AI Technical Summary
Problems solved by technology
Method used
Image
Examples
Embodiment 1
[0018] The molten iron is pretreated before entering the converter. After the treatment, the sulfur content of the molten iron is [S]=0.013%, and the temperature is 1298 °C. Before the molten iron enters the converter, the slag from the pretreatment of the molten iron is removed. After the first furnace before BOF smelting, empty out the remaining steel residue in the BOF, add molten iron and steel scrap to BOF smelting, 136t of molten iron, 15t of scrap steel, the carbon content in the molten iron is 4.86%, and the Si content is 0.46%.
[0019] The converter smelting process is controlled in accordance with conventional requirements for steel grades. The end point temperature of the converter is 1628 °C, the end point oxygen content is 530 ppm, and the end point carbon content is 0.076%. 5min, during the tapping process, pour 200kg of lime into the ladle, and 300kg of refined synthetic slag. No deoxidation and alloying operations are performed during tapping. After tapping, th...
Embodiment 2
[0021] The molten iron is pretreated before entering the converter. After the treatment, the sulfur content of the molten iron is [S]=0.012%, and the temperature is 1295 °C. Before the molten iron enters the converter, the pretreated slag is removed. After the first furnace before BOF smelting, empty the residual steel residue in the BOF, add molten iron and steel scrap for BOF smelting, 133t of molten iron, 16t of scrap steel, the carbon content in the molten iron is 4.67%, and the Si content is 0.44%.
[0022] The converter smelting process control is operated according to the conventional steel grades. The end point temperature of the converter is 1636 ℃, the end point oxygen content is 546 ppm, and the end point carbon content is 0.065%. The tapping time is 5 minutes. During the tapping process, 230 kg of lime and 310 kg of synthetic slag are poured into the ladle. No deoxidation and alloying operations are performed during tapping. Large argon gas stirring operation is per...
PUM
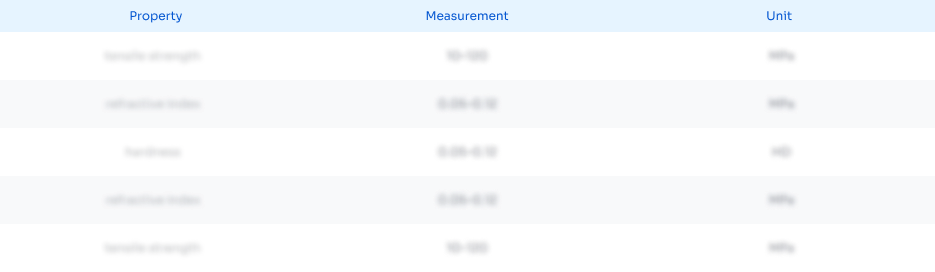
Abstract
Description
Claims
Application Information

- Generate Ideas
- Intellectual Property
- Life Sciences
- Materials
- Tech Scout
- Unparalleled Data Quality
- Higher Quality Content
- 60% Fewer Hallucinations
Browse by: Latest US Patents, China's latest patents, Technical Efficacy Thesaurus, Application Domain, Technology Topic, Popular Technical Reports.
© 2025 PatSnap. All rights reserved.Legal|Privacy policy|Modern Slavery Act Transparency Statement|Sitemap|About US| Contact US: help@patsnap.com