Method for uniformly fluorinating zinc oxide powder
A technology of zinc oxide and zinc oxide powder, which is applied in the direction of zinc oxide/zinc hydroxide, nanotechnology, etc., can solve the problems of complex process and expensive modifier, achieve strong bonding, improve surface properties, improve The effect of interface interaction
- Summary
- Abstract
- Description
- Claims
- Application Information
AI Technical Summary
Problems solved by technology
Method used
Image
Examples
Embodiment 1
[0022] A method for uniformly fluorinating zinc oxide powder, the following steps are adopted:
[0023] (1) Zinc oxide powder surface coupling agent treatment: Add zinc oxide powder with a particle size of 10nm to the mixture of titanate coupling agent NDZ-101 and alcohol, in which titanate coupling agent NDZ-101 The mass ratio of alcohol to alcohol is 1:10, treated at 90°C for 5 hours, cleaned with deionized water and alcohol, and dried in a drying oven for 2 hours;
[0024] (2) Polyvinyl alcohol coating treatment on the surface of zinc oxide powder: place the zinc oxide powder treated in the first step in polyvinyl alcohol aqueous solution, where the concentration of polyvinyl alcohol aqueous solution is 5%, zinc oxide powder and The mass ratio of the polyvinyl alcohol aqueous solution is 1:1, stirred at 50°C for 5 hours, then centrifuged, then centrifuged, and deionized water to wash to obtain fluorinated zinc oxide powder coated with polyvinyl alcohol on the surface;
[0...
Embodiment 2
[0029] A method for uniformly fluorinating zinc oxide powder, the following steps are adopted:
[0030] (1) Zinc oxide powder surface coupling agent treatment: Add zinc oxide powder with a particle size of 20 μm to the mixture of titanate coupling agent NDZ-101 and alcohol, in which titanate coupling agent NDZ-101 The mass ratio of alcohol to alcohol is 1:15, treated at 100°C for 3 hours, cleaned with deionized water and alcohol, and dried in a drying oven for 2 hours;
[0031] (2) Polyvinyl alcohol coating treatment on the surface of zinc oxide powder: place the zinc oxide powder treated in the first step in a polyvinyl alcohol aqueous solution, where the concentration range of the polyvinyl alcohol aqueous solution is 20%, and the zinc oxide powder The mass ratio of polyvinyl alcohol to aqueous solution is 1:5, stirred at 80°C for 1 hour, then centrifuged, then washed with deionized water to obtain fluorinated zinc oxide powder coated with polyvinyl alcohol on the surface ;...
Embodiment 3
[0034] The method is the same as in Example 2, except that zinc oxide powder with a particle size of 5 μm is used to obtain zinc oxide powder with surface fluorination treatment.
PUM
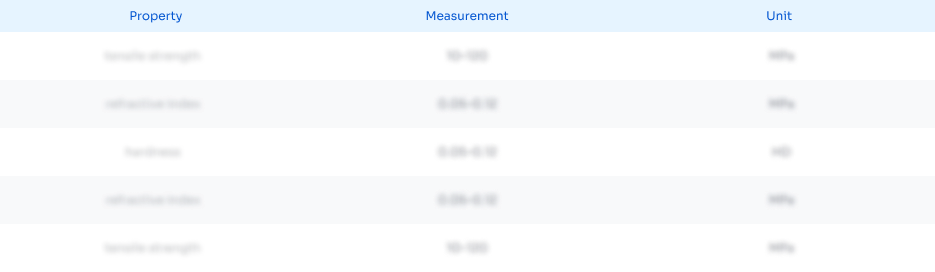
Abstract
Description
Claims
Application Information

- R&D Engineer
- R&D Manager
- IP Professional
- Industry Leading Data Capabilities
- Powerful AI technology
- Patent DNA Extraction
Browse by: Latest US Patents, China's latest patents, Technical Efficacy Thesaurus, Application Domain, Technology Topic, Popular Technical Reports.
© 2024 PatSnap. All rights reserved.Legal|Privacy policy|Modern Slavery Act Transparency Statement|Sitemap|About US| Contact US: help@patsnap.com