A kind of manufacturing method of non-magnetic cubic texture cu-ni-cr alloy base tape for high temperature superconducting coated conductor
A cu-ni-cr, coated conductor technology, applied in the field of high-temperature superconducting coated conductor metal baseband, can solve the problems of high Ni alloy cost, sharp cubic texture, limited use, etc., to improve oxidation resistance capacity, reduce consumption, and reduce investment cost
- Summary
- Abstract
- Description
- Claims
- Application Information
AI Technical Summary
Problems solved by technology
Method used
Image
Examples
Embodiment 1
[0023] According to Table 1, the composition is smelted and cast into billets, forged or hot-rough rolled into slabs, and then hot-rolled to form 1-10mm hot-rolled plates, cold-rolled and annealed in one stage under pure hydrogen, specifically cold-rolled, The annealing process, cubic texture volume fraction and high-temperature oxidation resistance are shown in Table 2. The high-temperature oxidation resistance test temperature is 800°C and the time is 1h.
[0024] Table 1. List of chemical components
[0025] Element Cu Ni Cr A 12 73 15 B 30 56 14 C 47 40 13 D 54 35 11 E 19 72 9 F 58 34 8 G 24 69 7 H 60 25 5
[0026] Table 2. List of cold rolling and one-stage annealing processes
[0027]
Embodiment 2
[0029] According to Table 1, the components are smelted and cast into slabs, forged or hot-rough-rolled into slabs, and then hot-rolled to form 1-10mm hot-rolled sheets, which are cold-rolled with a reduction ratio of 98% and two-stage annealing , see Table 3 for the specific annealing process and cubic texture volume fraction.
[0030] Table 3. List of two-stage annealing processes
[0031]
Embodiment 3
[0033] According to Table 1, the composition is smelted and cast into billets, forged or hot-rough-rolled into slabs, and then hot-rolled to form 1-10mm hot-rolled sheets, cold-rolled at a reduction rate of 96% and annealed in one stage. The annealing temperature was 1040°C, and the annealing time was 120 min. See Table 4 for the specific annealing atmosphere and cubic texture volume fraction.
[0034] Table 4. Annealing atmosphere list
[0035] Element Hot rolled plate thickness / mm Hydrogen ratio / % Nitrogen ratio / % Argon ratio / % Finished product thickness / mm Cubic Texture Fraction / % C 1 10 80 10 0.04 >96 D 2 10 90 0 0.08 >96 E 4 5 5 90 0.16 >96 F 6 30 10 60 0.24 >96 G 8 90 5 5 0.32 >96 H 3 100 0 0 0.12 >96 A 7 0 100 0 0.28 >96 B 10 0 0 100 0.4 >96 C 6 30 40 30 0.24 >96 D 6 15 15 70 0.24 >96 E 6 80 20 0 0.24 >96
PUM
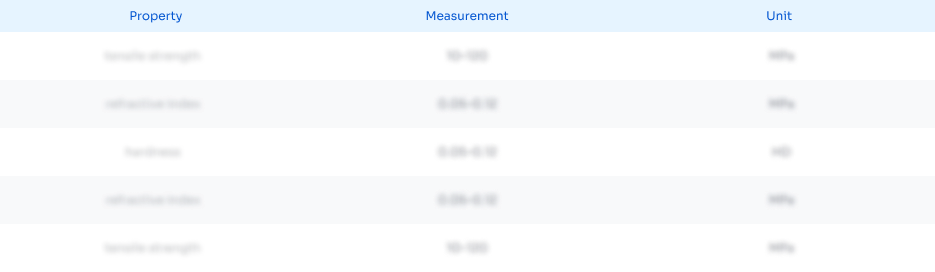
Abstract
Description
Claims
Application Information

- Generate Ideas
- Intellectual Property
- Life Sciences
- Materials
- Tech Scout
- Unparalleled Data Quality
- Higher Quality Content
- 60% Fewer Hallucinations
Browse by: Latest US Patents, China's latest patents, Technical Efficacy Thesaurus, Application Domain, Technology Topic, Popular Technical Reports.
© 2025 PatSnap. All rights reserved.Legal|Privacy policy|Modern Slavery Act Transparency Statement|Sitemap|About US| Contact US: help@patsnap.com