Method for preparing nanometer magnesium aluminum spinel
A magnesia-aluminum spinel and aluminum spinel technology, which is applied in the field of preparing nano-magnesium-aluminum spinel, can solve the problems of decreased specific surface area, imperfect crystallization of magnesia-aluminum spinel particles, poor stability and the like, and achieves perfect crystallization , easy to mass production, solve the effect of agglomeration and sintering
- Summary
- Abstract
- Description
- Claims
- Application Information
AI Technical Summary
Problems solved by technology
Method used
Image
Examples
Embodiment 1
[0038] Example 1: Prepare 2 L of potassium sulfate solution with a concentration of 0.1 mol / L with deionized water, add polyacrylic acid with a salt mass of 5%, and dissolve it. Under the condition of stirring, drop the potassium sulfate solution containing polyacrylic acid into 50 liters of ethanol, wash the precipitate with ethanol for 1-2 times, and obtain nanometer potassium sulfate after drying. Weigh 20 grams of nano-potassium sulfate, disperse it in 200 ml of ethanol, add 0.5 grams of stearic acid, and keep stirring at 50° C. for 2 hours. After centrifuging the nano-potassium sulfate ethanol dispersion, disperse the nano-potassium sulfate in 200ml xylene, add 10g magnesium aluminum carbonate precursor, stir at 80°C for 2 hours, centrifuge, dry, calcinate at 1000°C for 2 hours, wash with water and drying to obtain nano-magnesium-aluminum spinel.
Embodiment 2
[0039] Example 2: Prepare 2 L of potassium sulfate solution with a concentration of 0.1 mol / L with deionized water, add polyacrylic acid with a salt mass of 5%, and dissolve it. Under the condition of stirring, drop the potassium sulfate solution containing polyacrylic acid into 50 liters of ethanol, wash the precipitate with ethanol for 1-2 times, and obtain nanometer potassium sulfate after drying. Weigh 0.2 g of nano-potassium sulfate, disperse it in 200 ml of ethanol, add 0.02 g of stearic acid, and keep stirring at 50° C. for 2 hours. After centrifuging the nano potassium sulfate ethanol dispersion, disperse the nano potassium sulfate in 200ml xylene, add 0.1g magnesium aluminum carbonate precursor, stir at 80°C for 2 hours, centrifuge, dry, and calcinate at 1000°C for 2 hours, After washing with water and drying, the nano-magnesium-aluminum spinel is obtained.
Embodiment 3
[0040]Example 3: Prepare 2 L of potassium sulfate solution with a concentration of 0.1 mol / L with deionized water, add polyacrylic acid with a salt mass of 5%, and dissolve it. Under the condition of stirring, drop the potassium sulfate solution containing polyacrylic acid into 50 liters of ethanol, wash the precipitate with ethanol for 1-2 times, and obtain nanometer potassium sulfate after drying. Weigh 10 grams of nano-potassium sulfate, disperse it in 200 ml of ethanol, add 0.5 grams of stearic acid, and keep stirring at 50° C. for 2 hours. After centrifuging the nano-potassium sulfate ethanol dispersion, disperse the nano-potassium sulfate in 200ml xylene, add 5g magnesium aluminum carbonate precursor, stir at 80°C for 2 hours, centrifuge, dry, calcinate at 1000°C for 2 hours, wash with water and drying to obtain nano-magnesium-aluminum spinel.
PUM
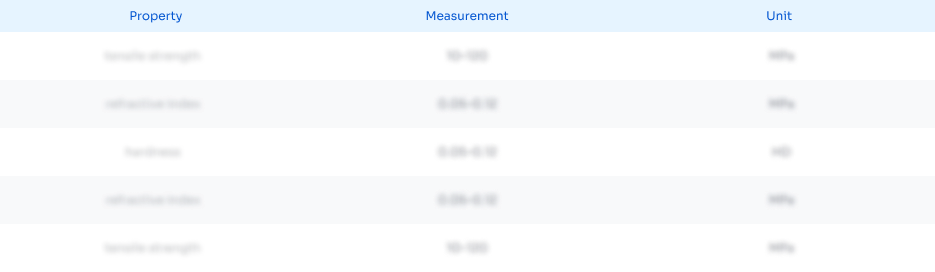
Abstract
Description
Claims
Application Information

- Generate Ideas
- Intellectual Property
- Life Sciences
- Materials
- Tech Scout
- Unparalleled Data Quality
- Higher Quality Content
- 60% Fewer Hallucinations
Browse by: Latest US Patents, China's latest patents, Technical Efficacy Thesaurus, Application Domain, Technology Topic, Popular Technical Reports.
© 2025 PatSnap. All rights reserved.Legal|Privacy policy|Modern Slavery Act Transparency Statement|Sitemap|About US| Contact US: help@patsnap.com