Al-Zn-Mn alloy profile for rail transit vehicle body and preparation method thereof
A technology for rail transit and alloy profiles, applied in the fields of metal materials and their processing, and aluminum alloy processing, which can solve the problems of low alloy toughness, fatigue resistance and stress corrosion resistance, hydrogen and slag content cannot be effectively controlled, and it is difficult to meet high-speed EMU and other problems, to reduce the tendency of cracking and deformation, reduce the amount of head and tail removal, and improve the service life
- Summary
- Abstract
- Description
- Claims
- Application Information
AI Technical Summary
Problems solved by technology
Method used
Image
Examples
Embodiment 1
[0033] A method for preparing a high-strength, toughness, and corrosion-resistant Al-Zn-Mg aluminum alloy profile for a rail transit car body comprises the following steps:
[0034](1) Smelting: Mix various raw materials according to the mass percentage, the chemical composition is: Zn4.4%, the mass percentage ratio of Zn and Mg is 3.2; Cu0.1%, Mn0.3%, Cr0.16%, Ti0 .04%, Zr0.12%, Fe≤0.12%, Si≤0.06%, and the balance is Al. Heat to 760°C to melt the material and keep it warm for 5 hours; add Al-Ti-C as the master alloy for grain refinement.
[0035] (2) Degassing and filtering: Degas the molten aluminum after degassing, and then filter to remove the insoluble matter in the molten aluminum;
[0036] (3) Casting: pour the degassed and filtered aluminum liquid, cool it to room temperature, and obtain a round ingot with a diameter of 390mm;
[0037] (4) Soaking heat treatment: place the cast ingot in a soaking furnace for heating and heat preservation, and perform homogenizing hea...
Embodiment 2
[0044] A method for preparing a high-strength, toughness, and corrosion-resistant Al-Zn-Mg aluminum alloy profile for a rail transit car body comprises the following steps:
[0045] (1) Melting: Mix various raw materials according to the mass percentage, the chemical composition is: Zn: 4.6%, the mass percentage ratio of Zn and Mg is 3.5; Cu: 0.15%, Mn: 0.4%, Cr: 0.24%, Ti :0.08%, Zr:0.20%, Fe≤0.12%, Si≤0.06%, and the balance is Al. Heat to 780°C to melt the material and keep it warm for 7 hours; add Al-Ti-C as the master alloy for grain refinement.
[0046] (2) Degassing and filtering: Degas the molten aluminum after degassing, and then filter to remove the insoluble matter in the molten aluminum;
[0047] (3) Casting: pour the degassed and filtered aluminum liquid, cool it to room temperature, and obtain a round ingot with a diameter of 580mm;
[0048] (4) Soaking heat treatment: place the cast ingot in a soaking furnace for heating and heat preservation, and perform homog...
Embodiment 3
[0055] A method for preparing a high-strength, toughness, and corrosion-resistant Al-Zn-Mg aluminum alloy profile for a rail transit car body comprises the following steps:
[0056] (1) Melting: Mix various raw materials according to the mass percentage, the chemical composition is: Zn: 4.5%, the mass percentage ratio of Zn and Mg is 3.3; Cu: 0.12%, Mn: 0.32%, Cr: 0.20%, Ti :0.06%, Zr:0.16%, Fe≤0.12%, Si≤0.06%, and the balance is Al. Heat to 770°C to melt the material and keep it warm for 6 hours; add Al-Ti-C as the master alloy for grain refinement.
[0057] (2) Degassing and filtering: Degas the molten aluminum after degassing, and then filter to remove the insoluble matter in the molten aluminum;
[0058] (3) Casting: pour the degassed and filtered aluminum liquid, cool it to room temperature, and obtain a round ingot with a diameter of 460mm;
[0059] (4) Soaking heat treatment: place the cast ingot in a soaking furnace for heating and heat preservation, and perform homo...
PUM
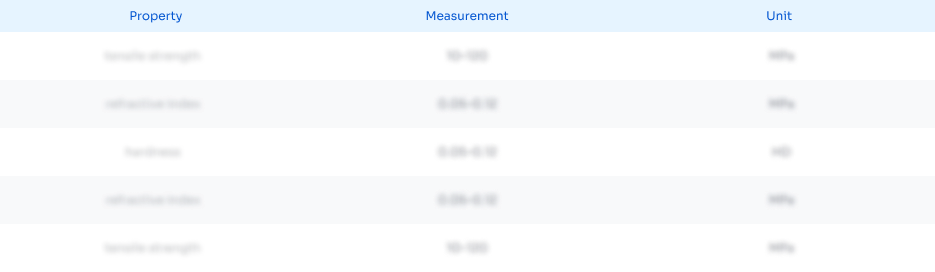
Abstract
Description
Claims
Application Information

- Generate Ideas
- Intellectual Property
- Life Sciences
- Materials
- Tech Scout
- Unparalleled Data Quality
- Higher Quality Content
- 60% Fewer Hallucinations
Browse by: Latest US Patents, China's latest patents, Technical Efficacy Thesaurus, Application Domain, Technology Topic, Popular Technical Reports.
© 2025 PatSnap. All rights reserved.Legal|Privacy policy|Modern Slavery Act Transparency Statement|Sitemap|About US| Contact US: help@patsnap.com