Formula of water-based dip-coating coating special for precoated sand
A coated sand and water-based technology, applied in coatings, casting molding equipment, casting molds, etc., can solve the problem of poor anti-sticking and anti-sand ability of coatings, limited sources of raw materials for coatings, lack of zircon powder resources, etc. problems, achieve superior light resistance, prevent precipitation, and improve surface quality
- Summary
- Abstract
- Description
- Claims
- Application Information
AI Technical Summary
Problems solved by technology
Method used
Examples
Embodiment 1
[0024] Embodiment 1 A kind of formula of water-based dip-coating coating special for coated sand, comprising refractory aggregate, binding agent, suspending agent, surfactant and carrier;
[0025] The parts by weight of each raw material in the refractory aggregate are: 20 parts by weight of mullite, 7 parts by weight of red iron oxide, 18 parts by weight of lithium limestone and 5 parts by weight of ball clay powder;
[0026] The parts by weight of each raw material in the binder are respectively: 1.0 parts by weight of polyvinyl alcohol and 1.2 parts by weight of silica sol;
[0027] The parts by weight of each raw material in the suspending agent are respectively: 2 parts by weight of lithium-based bentonite and 1.5 parts by weight of magnesium aluminum silicate;
[0028] The parts by weight of each raw material in the surfactant are respectively: 0.2 parts by weight of water-based defoamer, 0.1 part by weight of wetting agent and 0.1 part by weight of penetrant;
[0029] ...
Embodiment 2
[0031] Embodiment 2 A special water-based dip-coating paint formulation for coated sand, including refractory aggregate, binding agent, suspending agent, surfactant and carrier;
[0032] The parts by weight of each raw material in the refractory aggregate are respectively: 23 parts by weight of mullite, 10 parts by weight of red iron oxide, 22 parts by weight of lithium limestone and 8 parts by weight of spherical clay powder;
[0033] The parts by weight of each raw material in the binder are respectively: 2.2 parts by weight of polyvinyl alcohol and 1.5 parts by weight of silica sol;
[0034] The parts by weight of each raw material in the suspending agent are respectively: 3 parts by weight of lithium-based bentonite and 2.5 parts by weight of magnesium aluminum silicate;
[0035] The parts by weight of each raw material in the surfactant are respectively: 0.3 parts by weight of water-based defoamer, 0.2 parts by weight of wetting agent and 0.15 parts by weight of penetrant...
Embodiment 3
[0038] Example 3 A formulation of water-based dip coating for coated sand, including refractory aggregates, binders, suspending agents, surfactants and carriers;
[0039] The parts by weight of each raw material in the refractory aggregate are respectively: 21 parts by weight of mullite, 8 parts by weight of red iron oxide, 20 parts by weight of lithium limestone and 6 parts by weight of spherical clay powder;
[0040] The parts by weight of each raw material in the binder are respectively: 1.6 parts by weight of polyvinyl alcohol and 1.3 parts by weight of silica sol;
[0041] The parts by weight of each raw material in the suspending agent are respectively: 2.5 parts by weight of lithium-based bentonite and 2 parts by weight of magnesium aluminum silicate;
[0042] The parts by weight of each raw material in the surfactant are respectively: 0.25 parts by weight of water-based defoamer, 0.15 parts by weight of wetting agent and 0.12 parts by weight of penetrant;
[0043] The...
PUM
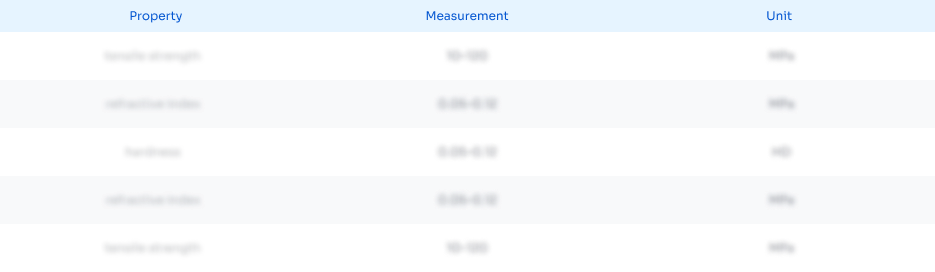
Abstract
Description
Claims
Application Information

- Generate Ideas
- Intellectual Property
- Life Sciences
- Materials
- Tech Scout
- Unparalleled Data Quality
- Higher Quality Content
- 60% Fewer Hallucinations
Browse by: Latest US Patents, China's latest patents, Technical Efficacy Thesaurus, Application Domain, Technology Topic, Popular Technical Reports.
© 2025 PatSnap. All rights reserved.Legal|Privacy policy|Modern Slavery Act Transparency Statement|Sitemap|About US| Contact US: help@patsnap.com