Secondary refining method capable of improving cleanliness of molten steel
A technology of secondary refining and cleanliness, which is applied in the field of metallurgy and can solve problems such as not being universally applicable
- Summary
- Abstract
- Description
- Claims
- Application Information
AI Technical Summary
Problems solved by technology
Method used
Image
Examples
Embodiment 1
[0013] Embodiment 1 (the 1st pot of pouring order):
[0014] (1) The carbon content at the control end point of converter tapping is 0.35%, the phosphorus content is 0.012%, and the sulfur content is 0.026%. Add recarburizer, ferrosilicon manganese and high-carbon ferromanganese when tapping the steel, the tapping temperature is 1658°C, and add 230kg of lidded lime after tapping;
[0015] (2) The steel ladle is transported to the LF station, and the entry temperature is 1577°C. The LF process performs desulfurization, alloying, heating and stirring operations according to the requirements of the steel type. After the temperature and alloy are all adjusted, slaked lime is added from the high-level silo at one time. 800kg, followed by a weak argon blowing operation for 4 minutes, after the argon blowing is completed, add 320kg of thick slag lime, after adding, hoist from the LF station to the VD station;
[0016] (3) After entering the VD, vacuumize the furnace to degas the fur...
Embodiment 2
[0017] Embodiment 2 (pouring the 6th can):
[0018] (1) The carbon content at the end point of converter tapping control is 0.39%, the phosphorus content is 0.013%, and the sulfur content is 0.029%. Add recarburizer, silicomanganese ferromanganese and high carbon ferromanganese when tapping, the tapping temperature is 1655℃, after tapping, add 240kg of lid can lime;
[0019] (2) The ladle is transported to the LF station, and the entry temperature is 1572°C. The LF process performs desulfurization, alloying, heating and stirring operations according to the requirements of the steel type. After the temperature and alloy are all adjusted, slaked lime is added from the high-level silo at one time. 860kg, followed by a weak argon blowing operation for 4 minutes, after the argon blowing is completed, add 350kg of thick slag lime, after adding, hoist from the LF station to the VD station;
[0020] (3) After entering the VD, vacuumize the furnace for degassing. The pressure holding ...
Embodiment 3
[0021] Embodiment 3 (the 7th pot of pouring time):
[0022] (1) The carbon content at the control end point of converter tapping is 0.42%, the phosphorus content is 0.015%, and the sulfur content is 0.027%. Add recarburizer, silicomanganese ferromanganese and high carbon ferromanganese when tapping, the tapping temperature is 1654℃, after tapping, add 280kg of lid can lime;
[0023] (2) The steel ladle is transported to the LF station, and the entry temperature is 1571°C. The LF process performs desulfurization, alloying, heating and stirring operations according to the requirements of the steel type. After the temperature and alloy are all adjusted, slaked lime is added from the high-level silo at one time. 870kg, followed by weak argon blowing operation for 5 minutes, after argon blowing, add 380kg of thick slag lime, after adding, hoist from LF station to VD station;
[0024] (3) After entering the VD, vacuumize the furnace to degas the furnace. The pressure holding time o...
PUM
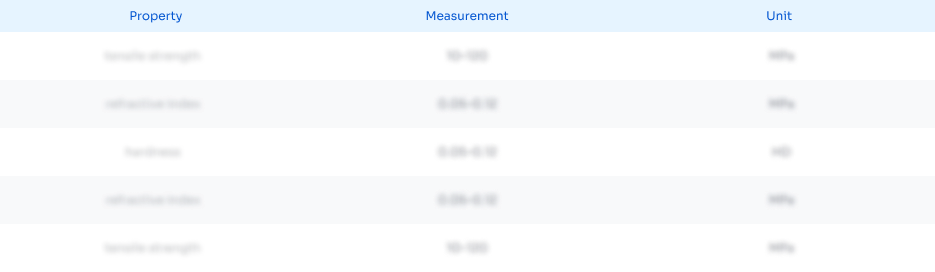
Abstract
Description
Claims
Application Information

- Generate Ideas
- Intellectual Property
- Life Sciences
- Materials
- Tech Scout
- Unparalleled Data Quality
- Higher Quality Content
- 60% Fewer Hallucinations
Browse by: Latest US Patents, China's latest patents, Technical Efficacy Thesaurus, Application Domain, Technology Topic, Popular Technical Reports.
© 2025 PatSnap. All rights reserved.Legal|Privacy policy|Modern Slavery Act Transparency Statement|Sitemap|About US| Contact US: help@patsnap.com