Novel production process of plastic woven bag
A technology of plastic woven bag and production process, applied in the field of plastic woven bag production process, can solve the problems of poor heat resistance, poor weather resistance, dull appearance of woven bags, calcium carbonate dust pollution, etc., so as to improve comprehensive performance and reduce fluff and splitting. , the effect of improving the service life
- Summary
- Abstract
- Description
- Claims
- Application Information
AI Technical Summary
Problems solved by technology
Method used
Image
Examples
Embodiment 1
[0016] Embodiment 1, the present invention comprises the following steps,
[0017] 1) Mixing of raw materials:
[0018] Comprise A component, A component comprises following raw material, polypropylene, maleic anhydride, styrene, xylene, dicumyl peroxide, wherein the weight ratio of polypropylene, maleic anhydride, styrene is 25:1: 1,
[0019] The synthesis method of component A is: put polypropylene, maleic anhydride, and a small amount of xylene in a stirred reactor and gradually raise the temperature. When the temperature rises to 100-110°C, add dicumyl peroxide, and heat up to 120-130°C. When adding styrene, then keep 120 ~ 130 ° C for 2 ~ 4 hours,
[0020] Also includes B component, B component includes the following raw materials in weight percentage, polypropylene 50%, polyethylene 30%, talcum powder 18%, phosphate ester dispersant 1%, ultraviolet quencher NBC 1%,
[0021] Send component A and component B into a drying mixer at a weight ratio of 1:20, the drying temp...
Embodiment 2
[0028] Embodiment 2, the present invention comprises the following steps,
[0029] 1) Mixing of raw materials:
[0030] Comprise A component, A component comprises following raw material, polypropylene, maleic anhydride, styrene, xylene, dicumyl peroxide, wherein the weight ratio of polypropylene, maleic anhydride, styrene is 25:1: 1,
[0031] The synthesis method of component A is as follows: put polypropylene, maleic anhydride, and xylene in a stirred reactor and gradually raise the temperature. When the temperature rises to 100-110°C, add dicumyl peroxide. Add styrene, then keep at 120-130°C for 2-4 hours,
[0032] Also includes B component, B component includes the following raw materials by weight percentage, polypropylene 55%, polyethylene 25%, talcum powder 16%, phosphate ester dispersant 2%, ultraviolet quencher NBC 2%,
[0033] Send component A and component B into a drying mixer at a weight ratio of 1:20, the drying temperature is 30-35°C, and the drying time is 1...
Embodiment 3
[0036] Embodiment 3, the present invention comprises the following steps,
[0037] 1) Mixing of raw materials:
[0038] Comprise A component, A component comprises following raw material, polypropylene, maleic anhydride, styrene, xylene, dicumyl peroxide, wherein the weight ratio of polypropylene, maleic anhydride, styrene is 25:1: 1,
[0039] The synthesis method of component A is as follows: put polypropylene, maleic anhydride, and xylene in a stirred reactor and gradually raise the temperature. When the temperature rises to 100-110°C, add dicumyl peroxide. Add styrene, then keep at 120-130°C for 2-4 hours,
[0040] Also includes B component, B component includes the following raw materials in weight percentage, polypropylene 51%, polyethylene 30%, talcum powder 15%, phosphate ester dispersant 2%, ultraviolet quencher NBC 2%,
[0041] Send component A and component B into a drying mixer at a weight ratio of 1:20, the drying temperature is 30-35°C, and the drying time is 1...
PUM
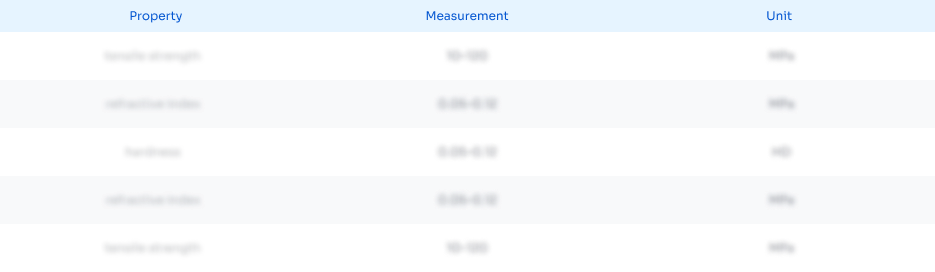
Abstract
Description
Claims
Application Information

- R&D Engineer
- R&D Manager
- IP Professional
- Industry Leading Data Capabilities
- Powerful AI technology
- Patent DNA Extraction
Browse by: Latest US Patents, China's latest patents, Technical Efficacy Thesaurus, Application Domain, Technology Topic, Popular Technical Reports.
© 2024 PatSnap. All rights reserved.Legal|Privacy policy|Modern Slavery Act Transparency Statement|Sitemap|About US| Contact US: help@patsnap.com