Preparation method for composite fluorescent glass cover
A composite fluorescent and glass cover technology, which is applied in glass manufacturing equipment, glass molding, chemical instruments and methods, etc., can solve the problem of increasing the radiation of red light in luminescent materials, small thermal conductivity of epoxy resin, and poor coating of fluorescent materials. Uniformity and other issues to achieve the effect of improving the effective utilization capacity, solving aging yellowing, and enhancing the intensity of fluorescent light
- Summary
- Abstract
- Description
- Claims
- Application Information
AI Technical Summary
Problems solved by technology
Method used
Examples
example 1
[0020] Add 0.10 mol of tetraethyl orthosilicate to 50 mL of absolute ethanol, stir at 300 r / min for 20 min, adjust the pH to 3 with a 5% nitric acid solution, and stir at 30°C for 1 h to obtain a pre-hydrolyzed solution. Take 0.003 mol Add europium nitrate, 0.001mol bismuth nitrate, 0.092mol yttrium nitrate, 0.10mol aluminum nitrate, 0.10mol zinc nitrate, 0.10mol tellurium oxide into 1.0L deionized water, stir and heat at 300r / min to 80°C, keep stirring for 30min to obtain a mixture solution, add the mixed solution dropwise into the pre-hydrolyzed solution at 2mL / min, continue to stir at 200r / min until the dropwise addition is complete, continue to stir for 2h, and then place it at 25°C for 7 days to obtain a wet gel. Put the gel in a drying oven and dry at 40°C for 2 days to obtain a dry gel. Put the dry gel into a grinder and grind it for 1 hour, then put it into a resistance furnace, and raise the temperature to 850°C at a heating rate of 5°C / min. Insulated and melted for 2...
example 2
[0022] Add 0.11 mol of tetraethyl orthosilicate to 80 mL of absolute ethanol, stir at 350 r / min for 25 min, adjust the pH to 3 with a 5% nitric acid solution, and stir at 35°C for 1 h to obtain a pre-hydrolyzed solution. Take 0.004 mol Add europium nitrate, 0.002mol bismuth nitrate, 0.095mol yttrium nitrate, 0.11mol aluminum nitrate, 0.11mol zinc nitrate, 0.11mol tellurium oxide into 1.1L deionized water, stir and heat at 350r / min to 85°C, keep stirring for 35min to obtain a mixture solution, add the mixed solution dropwise into the pre-hydrolyzed solution at 2mL / min, continue to stir at 250r / min until the dropwise addition is complete, continue to stir for 2h, and then place it at 28°C for 8 days to obtain a wet gel. Place the gel in a drying oven and dry at 60°C for 2 days to obtain a xerogel. Put the xerogel in a grinder and grind it for 1 hour, then put it into a resistance furnace, and raise the temperature to 880°C at a heating rate of 5°C / min. Insulated and melted for 2...
example 3
[0024] Add 0.12 mol of tetraethyl orthosilicate to 100 mL of absolute ethanol, stir at 400 r / min for 30 min, adjust the pH to 4 with a 5% nitric acid solution, and stir at 40°C for 2 h to obtain a pre-hydrolyzed solution. Take 0.005 mol Add europium nitrate, 0.003mol bismuth nitrate, 0.096mol yttrium nitrate, 0.12mol aluminum nitrate, 0.12mol zinc nitrate, and 0.12mol tellurium oxide into 1.2L deionized water, stir and heat to 90°C at 400r / min, keep stirring for 40min to obtain a mixture solution, add the mixed solution dropwise to the pre-hydrolyzed solution at 3mL / min, continue to stir at 300r / min until the dropwise addition is complete, continue to stir for 3h, and then place it at 30°C for 10 days to obtain a wet gel. Put the gel in a drying oven and dry at 70°C for 3 days to obtain a dry gel. Put the dry gel into a grinder and grind it for 2 hours, then put it into a resistance furnace, and raise the temperature to 900°C at a heating rate of 5°C / min. Insulated and melted ...
PUM
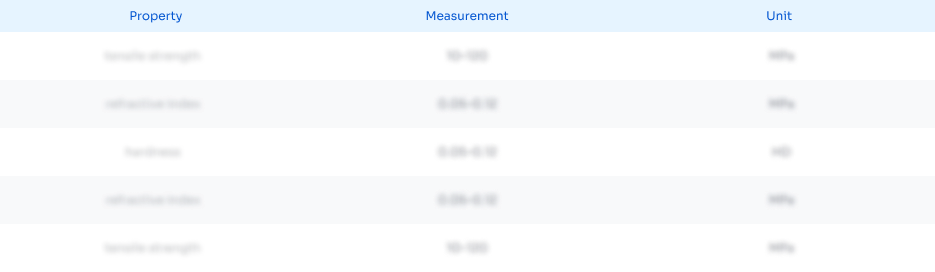
Abstract
Description
Claims
Application Information

- R&D Engineer
- R&D Manager
- IP Professional
- Industry Leading Data Capabilities
- Powerful AI technology
- Patent DNA Extraction
Browse by: Latest US Patents, China's latest patents, Technical Efficacy Thesaurus, Application Domain, Technology Topic, Popular Technical Reports.
© 2024 PatSnap. All rights reserved.Legal|Privacy policy|Modern Slavery Act Transparency Statement|Sitemap|About US| Contact US: help@patsnap.com