An internal heating type low temperature carbonization thermal state simulation detection device and method
A detection device and an endothermic technology, which are applied to the field of endothermic low-temperature dry distillation thermal state simulation detection devices, can solve the problems of long time for exploration, improvement and adjustment, easy slagging of flames, economic losses, etc. The effect of less investment and lower economic losses
- Summary
- Abstract
- Description
- Claims
- Application Information
AI Technical Summary
Problems solved by technology
Method used
Image
Examples
Embodiment 1
[0048] Example 1 The optimization of the dry distillation process of a low-temperature dry distillation enterprise with an annual output of 2.4 million tons of blue charcoal
[0049] (1) Basic situation:
[0050] There are 4 blue charcoal production plants with an annual processing capacity of 600,000 tons, using vertical square furnaces as basic production equipment, all-oxygen dry distillation process, and gas supply to downstream CNG production enterprises as raw gas. The size of the dry distillation chamber (furnace) is: length×width×height=6900×3500×7500mm. The gas composition is: H 2 40.07%, CO 16.08%, CO 2 13.15%, CH 4 14.21%, C2-C5 8.11%, the rest is nitrogen. Low calorific value of gas 5732kcal / m 3 . Slagging on the furnace wall at the fire hole occurred during production, which caused the furnace to be shut down for overhaul.
[0051] (2) Application method
[0052] According to the method of the present invention, enterprises build unit simulation test devices by them...
Embodiment 2
[0057] Example 2 Application of a blue charcoal production plant with an annual output of 1.2 million tons
[0058] (1) Basic situation:
[0059] Two blue charcoal production plants with an annual processing capacity of 600,000 tons are under construction, using vertical square furnaces as the basic production equipment, oxygen-enriched carbonization process, and the gas is supplied to the downstream synthetic ammonia production enterprises as raw gas, and the hydrogen-nitrogen ratio in the gas is maintained as required It is about 3.0 or more. The size of the dry distillation chamber (furnace) is: length×width×height=6800×3600×7200mm. With reference to the operation of related enterprises, the selected gas composition is: H 2 38.0%, CO 15.4%, CO 2 11.0%, CH 4 12.2%, C2-C5 2.11%, the rest is nitrogen. Gas low calorific value 5362kcal / m 3 . The design of the burner, the fire channel and the fire eye need to be thermally tested.
[0060] (2) Application method
[0061] According ...
Embodiment 3
[0065] Example 3 Application of a blue charcoal production plant with an annual output of 600,000 tons
[0066] (1) Basic situation
[0067] The vertical square furnace is used as the basic production equipment, air-assisted combustion, and the coal-coke ratio is 1.67:1. The tar production rate is about 7.8% (the Shenmu dry-based raw coal is the benchmark), and the remaining gas volume per ton of coal is 560m 3 Around (Shenmu coal), gas calorific value 1700-1900kcal / Nm 3 , The coal gas is consumed by small gas power generation. Lump coal is used as raw material into the furnace, and the particle size requirement is greater than 25mm. Due to the high price of lump coal and limited supply, which directly affects the normal operation and economic benefits of the enterprise, it is planned to reduce the particle size of the lump coal into the furnace to 10mm. What changes will happen to the furnace conditions at this time, especially what happens in the high temperature section The ch...
PUM
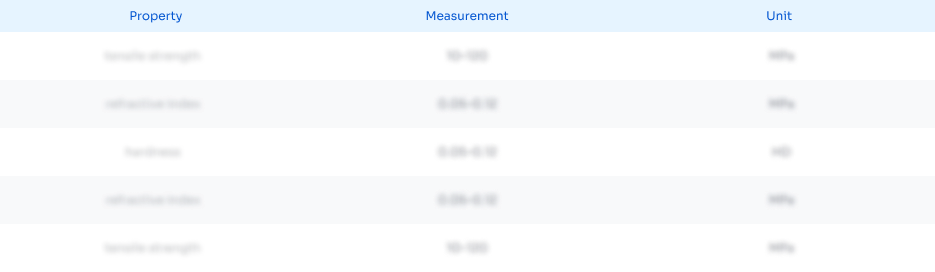
Abstract
Description
Claims
Application Information

- Generate Ideas
- Intellectual Property
- Life Sciences
- Materials
- Tech Scout
- Unparalleled Data Quality
- Higher Quality Content
- 60% Fewer Hallucinations
Browse by: Latest US Patents, China's latest patents, Technical Efficacy Thesaurus, Application Domain, Technology Topic, Popular Technical Reports.
© 2025 PatSnap. All rights reserved.Legal|Privacy policy|Modern Slavery Act Transparency Statement|Sitemap|About US| Contact US: help@patsnap.com