Method and device for carrying out 3D (Three-Dimensional) printing and composite manufacturing on metal
A technology of 3D printing and manufacturing method, applied in the field of 3D printing
- Summary
- Abstract
- Description
- Claims
- Application Information
AI Technical Summary
Problems solved by technology
Method used
Image
Examples
Embodiment approach
[0051] In the second specific embodiment provided by the present invention, the device includes: a worktable 1, a heat source generating mechanism 2, a metal powder feeding mechanism 3, a laser nozzle 4 and an ultrasonic vibrator 5; a heat source generating mechanism 2 and a metal powder feeding mechanism The mechanism 3 moves synchronously and is arranged above the upper surface of the workbench 1, so that the metal powder feeding mechanism 3 sprays the metal powder and is fused by the heat source generating mechanism 2 to form a cladding layer; the laser nozzle 4 and the heat source generating mechanism 2 move synchronously And it is arranged above the upper surface of the workbench 1, so that the laser nozzle 4 can impact and forge the cladding layer 6 with the shock wave induced by the laser shock; the ultrasonic vibrator 5 is arranged below the lower surface of the workbench 1, so that the ultrasonic The vibrator 1 impacts and forges the cladding layer 6 by utilizing ultra...
PUM
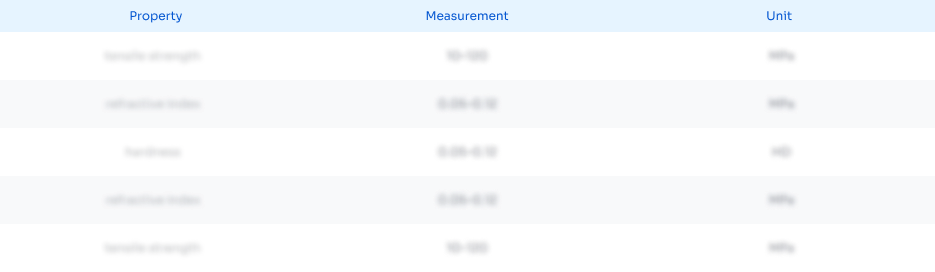
Abstract
Description
Claims
Application Information

- Generate Ideas
- Intellectual Property
- Life Sciences
- Materials
- Tech Scout
- Unparalleled Data Quality
- Higher Quality Content
- 60% Fewer Hallucinations
Browse by: Latest US Patents, China's latest patents, Technical Efficacy Thesaurus, Application Domain, Technology Topic, Popular Technical Reports.
© 2025 PatSnap. All rights reserved.Legal|Privacy policy|Modern Slavery Act Transparency Statement|Sitemap|About US| Contact US: help@patsnap.com