System and blending combustion method for coal-fired power station boiler for large-proportion blending combustion of semi-coke
A coal-fired power station, a large-scale technology, applied in the direction of combustion methods, combustion equipment, fuel supply, etc., can solve the problems of increased carbon content in fly ash, high emissions, and inability to operate at full load, and achieve improved ignition and combustion characteristics Effect
- Summary
- Abstract
- Description
- Claims
- Application Information
AI Technical Summary
Problems solved by technology
Method used
Image
Examples
Embodiment Construction
[0022] The present invention will be described in further detail below in conjunction with the accompanying drawings.
[0023] see figure 1 , the system of the present invention includes a boiler body 1 and an ignition zone 6, a semi-coke dense phase zone 7, a semi-coke light phase zone 8, a reburning zone 8 and a burnout zone 10 arranged from bottom to top in the furnace, and the bituminous coal passes through the bituminous coal Coal pulverizer 13 and reburning coal pulverizer 12 are respectively pulverized and then sent to the fire zone 6 and reburning zone 8; The semi-coke gas flow is sent to the semi-coke dense phase area 7 and the semi-coke light phase area 8 respectively; High volatile bituminous coal, and adopts direct-blowing powder feeding system, semi-coke uses hot air to feed powder, pure oxygen burn-off air is connected to burn-out zone 10, boiler flue is located at the upper end of oxygen preheater 5 and is equipped with blower 2 The connected air preheater 3, ...
PUM
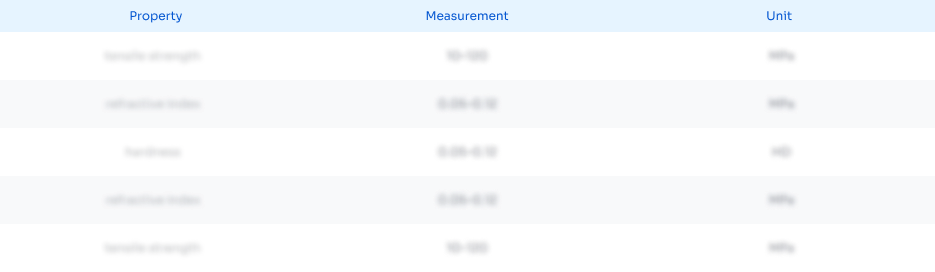
Abstract
Description
Claims
Application Information

- R&D
- Intellectual Property
- Life Sciences
- Materials
- Tech Scout
- Unparalleled Data Quality
- Higher Quality Content
- 60% Fewer Hallucinations
Browse by: Latest US Patents, China's latest patents, Technical Efficacy Thesaurus, Application Domain, Technology Topic, Popular Technical Reports.
© 2025 PatSnap. All rights reserved.Legal|Privacy policy|Modern Slavery Act Transparency Statement|Sitemap|About US| Contact US: help@patsnap.com