Method for reducing nitrogen oxide of powder coal boiler mixed burning gas fuel
A gas fuel and pulverized coal boiler technology, applied in the direction of combustion, burner, lighting and heating equipment using gaseous fuel and powder fuel, can solve the problems of excessive consumption of reburning fuel, affecting the formation of reducing atmosphere in the reburning zone, etc., to achieve Conducive to ignition and burnout, moderate initial investment and operating costs, and improved efficiency
- Summary
- Abstract
- Description
- Claims
- Application Information
AI Technical Summary
Problems solved by technology
Method used
Image
Examples
specific Embodiment approach 1
[0017] Specific implementation mode 1: The steps of the method for reducing nitrogen oxides by co-combusting gaseous fuel in pulverized coal boilers in this embodiment are as follows:
[0018] Step 1: Introduce primary gas fuel at the bottom of the main burner in the main combustion zone as a combustion-supporting fuel; increase the flue gas temperature in the main combustion zone to make the pulverized coal in the main combustion zone burn stably;
[0019] Step 2: Introduce secondary gas fuel at the top of the main combustion zone, form a reducing atmosphere in the reburning zone, and make the NO generated in the main combustion zone X When passing through the reburning zone, it is reduced by CHi, NHi, HCN, CO and other groups formed by the combustion of reburning fuel;
[0020] Step 3: Introduce the burnout air at the top of the reburning zone, so that the unburned products in the reburning zone are fully burned in the burnout zone above the reburning zone.
[0021] In this...
specific Embodiment approach 2
[0026] Specific embodiment two: In the method for reducing nitrogen oxides by co-combusting gas fuel in pulverized coal boilers in this embodiment, biomass gas is used as co-combusting gas, and biomass gas accounting for 10% of the boiler heat is introduced into the furnace at the lower part of the pulverized coal burner , the main combustion area adopts the horizontal thick-lean air combustion technology, the excess air coefficient in the main combustion area is controlled to 1.05, and the biomass gas, which accounts for 12% of the boiler heat, is introduced into the furnace at the upper part of the pulverized coal burner, and forms a reburning area with a reducing atmosphere. The excess air coefficient is 0.85, and groups such as CHi and NHi in the reburning zone reduce the NO generated in the main combustion zone X , the excess air coefficient in the burnout zone is 1.2.
specific Embodiment approach 3
[0027] Specific implementation mode three: In the method for reducing nitrogen oxides by co-combusting gas fuels in pulverized coal boilers in this embodiment, natural gas is used as co-combusting gas, and natural gas accounting for 10% of the boiler heat is introduced into the furnace at the lower part of the pulverized coal burner, and the main combustion zone The horizontal thick-lean air combustion technology is adopted, the excess air coefficient in the main combustion zone is controlled to 0.9, and the natural gas accounting for 10% of the boiler heat is introduced into the furnace at the upper part of the pulverized coal burner to form a reburning zone with a reducing atmosphere. The excess air coefficient in the reburning zone is 0.85, In the reburning zone CHi, HCN, NHi and other groups reduce the NO generated in the main combustion zone X , the excess air coefficient in the burnout zone is 1.2. The calorific value of natural gas is good, it is a good reburning fuel a...
PUM
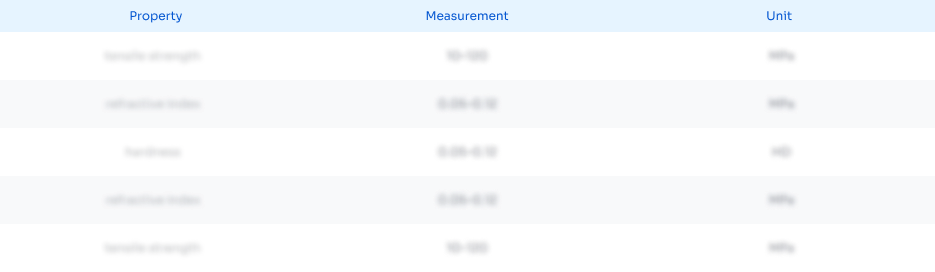
Abstract
Description
Claims
Application Information

- Generate Ideas
- Intellectual Property
- Life Sciences
- Materials
- Tech Scout
- Unparalleled Data Quality
- Higher Quality Content
- 60% Fewer Hallucinations
Browse by: Latest US Patents, China's latest patents, Technical Efficacy Thesaurus, Application Domain, Technology Topic, Popular Technical Reports.
© 2025 PatSnap. All rights reserved.Legal|Privacy policy|Modern Slavery Act Transparency Statement|Sitemap|About US| Contact US: help@patsnap.com