High-weather-resistance aluminum alloy sectional material
A technology of aluminum alloy profiles and high weather resistance, which is applied in the field of metal material manufacturing to achieve the effect of high safety and excellent tensile strength
- Summary
- Abstract
- Description
- Claims
- Application Information
AI Technical Summary
Problems solved by technology
Method used
Examples
Embodiment 1
[0031] A production method of high weather resistance aluminum alloy profiles:
[0032] (1) Ingredients and smelting:
[0033] Ingredients according to mass percentage: Zn 7%, Cu 1.5%, Fe 1%, Mn 3%, Mg 2%, Si 0.5%, Cr 0.2%, Ni 0.08%, Ti 0.03%, the rest is Al, smelting at 780°C for 6h , to obtain aluminum alloy melt;
[0034] (2) Casting:
[0035] Cast the obtained aluminum alloy solution at a temperature of 720°C and a casting speed of 70mn / min to form a cast rod, cut it into a short rod with a length of 600mm, remove the scale on its surface, and obtain an aluminum alloy ingot;
[0036] (3) Annealing:
[0037] Perform homogenizing annealing on the obtained aluminum alloy ingot at an annealing temperature of 460° C. for 25 hours;
[0038] (4) Two-step heat treatment:
[0039] The aluminum alloy ingot was placed in a resistance heating furnace for two-stage heating, the aluminum alloy ingot was heated to 350°C for 1 hour, and after air cooling, it was continued to be heate...
Embodiment 2
[0047] A production method of high weather resistance aluminum alloy profiles:
[0048] (1) Ingredients and melting:
[0049] Ingredients according to mass percentage: Zn 8.8%, Cu 0.8%, Fe 4%, Mn 2%, Mg 3%, Si 0.2%, Cr 0.8%, Ni 0.08%, Ti 0.03%, the rest is Al, smelting at 700°C 8h, obtain aluminum alloy melt;
[0050] (2) Casting:
[0051] Cast the obtained aluminum alloy solution at a temperature of 700°C and a casting speed of 85 mm / min to form a cast rod, cut into a short rod with a length of 500 mm, and remove the scale on its surface to obtain an aluminum alloy ingot;
[0052] (3) Annealing:
[0053] Perform homogenizing annealing on the obtained aluminum alloy ingot at an annealing temperature of 475° C. for 20 hours;
[0054] (4) Two-step heat treatment:
[0055] The aluminum alloy ingot was put into a resistance heating furnace for two-stage heating, the aluminum alloy ingot was heated to 350°C for 1 hour, and after air cooling, it was continued to be heated to 50...
Embodiment 3
[0063] A production method of high weather resistance aluminum alloy profiles:
[0064] (1) Ingredients and smelting:
[0065] Ingredients according to mass percentage: Zn 7.3%, Cu 1.4%, Fe 2%, Mn 3%, Mg 2%, Si 0.4%, Cr 0.6%, Ni 0.08%, Ti 0.03%, the rest is Al, smelting at 710°C 7h, obtain aluminum alloy melt;
[0066] (2) Casting:
[0067] Cast the obtained aluminum alloy solution at a temperature of 715°C and a casting speed of 78mn / min to form a cast rod, cut it into a short rod with a length of 535mm, remove the scale on its surface, and obtain an aluminum alloy ingot;
[0068] (3) Annealing:
[0069] Perform homogenizing annealing on the obtained aluminum alloy ingot at an annealing temperature of 463° C. for 23 hours;
[0070] (4) Two-step heat treatment:
[0071] The aluminum alloy ingot was placed in a resistance heating furnace for two-stage heating, the aluminum alloy ingot was heated to 350°C for 1 hour, and after air cooling, it was continued to be heated to 5...
PUM
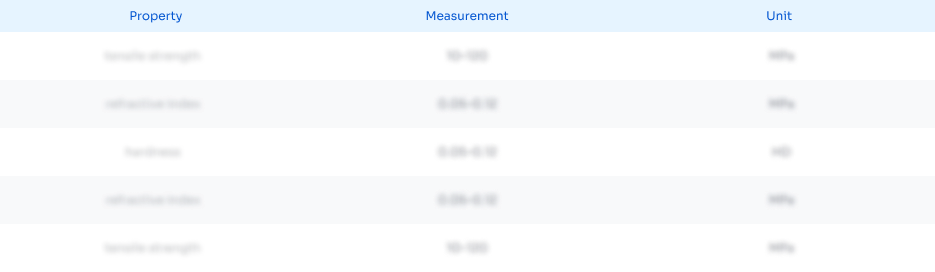
Abstract
Description
Claims
Application Information

- R&D
- Intellectual Property
- Life Sciences
- Materials
- Tech Scout
- Unparalleled Data Quality
- Higher Quality Content
- 60% Fewer Hallucinations
Browse by: Latest US Patents, China's latest patents, Technical Efficacy Thesaurus, Application Domain, Technology Topic, Popular Technical Reports.
© 2025 PatSnap. All rights reserved.Legal|Privacy policy|Modern Slavery Act Transparency Statement|Sitemap|About US| Contact US: help@patsnap.com