Nuclear Island Evaporator Kit Hole Forming Method
An evaporator and hole-forming technology, which is applied in the field of forging holes, can solve the problems of low production efficiency, the punch cannot be pulled out from the blank, it is difficult to heat through and compact, etc.
- Summary
- Abstract
- Description
- Claims
- Application Information
AI Technical Summary
Problems solved by technology
Method used
Examples
Embodiment Construction
[0022] Taking the lower head of the moving stack evaporator as an example, the lower head has a hemispherical spherical crown structure, and two coolant input pipe holes and two coolant output pipe holes are arranged on the main body of the lower head. The octagonal prism-shaped forged steel ingot is adopted, and the material of the ingot is martensitic heat-resistant steel P112.
[0023] First, the steel ingot is heated up in stages. First put the forged steel ingot into the heating furnace for heating to improve the plasticity of the metal, make it easy to flow form and obtain a good after-forging structure, choose the appropriate heating temperature range, and the metal blank can be formed in a state of better plasticity. Since the steel ingot is a large piece, in order to reduce the temperature stress caused by the temperature difference of the section, the steel ingot should be heated evenly. The present invention adopts the seven-stage heating standard. Keep warm for 3 ...
PUM
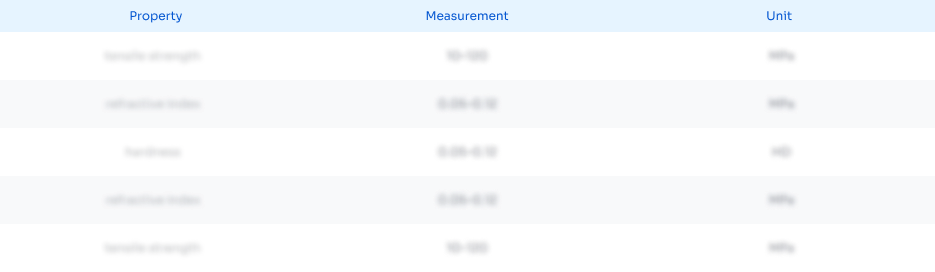
Abstract
Description
Claims
Application Information

- R&D
- Intellectual Property
- Life Sciences
- Materials
- Tech Scout
- Unparalleled Data Quality
- Higher Quality Content
- 60% Fewer Hallucinations
Browse by: Latest US Patents, China's latest patents, Technical Efficacy Thesaurus, Application Domain, Technology Topic, Popular Technical Reports.
© 2025 PatSnap. All rights reserved.Legal|Privacy policy|Modern Slavery Act Transparency Statement|Sitemap|About US| Contact US: help@patsnap.com