Preparation method of insulating material for electrical equipment
A technology for insulating materials and electrical equipment, applied in the direction of rubber insulators, organic insulators, plastic/resin/wax insulators, etc., can solve the problems of large air insulation volume, equipment insulation breakdown, and operation insulation accidents, and achieve high insulation resistance, Good flame retardant performance and the effect of reducing cold flow
- Summary
- Abstract
- Description
- Claims
- Application Information
AI Technical Summary
Problems solved by technology
Method used
Examples
Embodiment 1
[0023] A method for preparing an insulating material for electrical equipment, comprising the following preparation steps:
[0024] a. Mix waste rubber, epoxy resin and silicone rubber into a banbury mixer and banbury to a molten state. The temperature in the banbury mixer is 460°C, and then add flame retardant, nano-silica and carbon black in sequence, and The temperature was lowered to 240°C to obtain mixture 1;
[0025] b. Mix processing auxiliary materials, polyimide, sodium alginate, lignin and antioxidants in a mixer, heat at 90°C and perform ultrasonic stirring for 2 hours to obtain mixture 2;
[0026] c. Add silicone oil and coupling agent to mixture 2, place it in a stirrer and stir for 30 minutes, and then place it in a vacuum environment for degassing treatment for 15 minutes to obtain mixture 3;
[0027] d. Mix mixture 1, mixture 3, organotin and curing agent evenly and then import it into a single screw for extrusion, then import it into a dehydrator for dehydrat...
Embodiment 2
[0036] A method for preparing an insulating material for electrical equipment, comprising the following preparation steps:
[0037] a. Mix waste rubber, epoxy resin and silicone rubber into a banbury mixer and banbury to a molten state. The temperature in the banbury mixer is 580°C, and then add flame retardant, nano-silica and carbon black in sequence, and The temperature was lowered to 240°C to obtain mixture 1;
[0038] b. Mix processing auxiliary materials, polyimide, sodium alginate, lignin and antioxidants in a mixer, heat at 110°C and perform ultrasonic stirring for 2 hours to obtain mixture 2;
[0039] c. Add silicone oil and coupling agent to mixture 2, place it in a stirrer and stir for 40 minutes, and then place it in a vacuum environment for degassing treatment for 15 minutes to obtain mixture 3;
[0040] d. Mix mixture 1, mixture 3, organotin and curing agent evenly, then import it into a single screw for extrusion, then import it into a dehydrator for dehydratio...
Embodiment 3
[0049] A method for preparing an insulating material for electrical equipment, comprising the following preparation steps:
[0050]a. Mix waste rubber, epoxy resin and silicone rubber into a banbury mixer and banbury to a molten state. The temperature in the banbury mixer is 460°C, and then add flame retardant, nano-silica and carbon black in sequence, and The temperature was lowered to 180°C to obtain mixture 1;
[0051] b. Mix processing auxiliary materials, polyimide, sodium alginate, lignin and antioxidants in a mixer, heat at 90°C and perform ultrasonic stirring for 1 hour to obtain mixture 2;
[0052] c. Add silicone oil and coupling agent to mixture 2, place it in a stirrer and stir for 30-40 minutes, and then place it in a vacuum environment for degassing treatment for 10 minutes to obtain mixture 3;
[0053] d. Mix mixture 1, mixture 3, organotin and curing agent evenly and then import it into a single screw for extrusion, then import it into a dehydrator for dehydra...
PUM
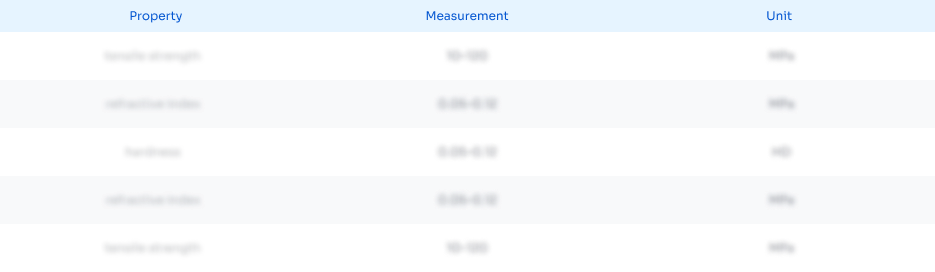
Abstract
Description
Claims
Application Information

- Generate Ideas
- Intellectual Property
- Life Sciences
- Materials
- Tech Scout
- Unparalleled Data Quality
- Higher Quality Content
- 60% Fewer Hallucinations
Browse by: Latest US Patents, China's latest patents, Technical Efficacy Thesaurus, Application Domain, Technology Topic, Popular Technical Reports.
© 2025 PatSnap. All rights reserved.Legal|Privacy policy|Modern Slavery Act Transparency Statement|Sitemap|About US| Contact US: help@patsnap.com