Thermal insulating mortar and preparation method thereof
A technology of thermal insulation mortar and hydrochloric acid, which is applied in ceramic products, other household appliances, household appliances, etc., can solve the problem of thermal conductivity, dry apparent density and shrinkage rate, unreasonable stirring process, stirring time, stirring intensity, and can not meet thermal insulation mortar. Special requirements and other issues to achieve the effect of shortening the curing and drying time, reducing the dry apparent density, and reducing the thermal conductivity
- Summary
- Abstract
- Description
- Claims
- Application Information
AI Technical Summary
Problems solved by technology
Method used
Image
Examples
Embodiment 1
[0024] A thermal insulation mortar, in parts by weight, comprising the following raw materials: 112 parts of Portland cement, 8 parts of fly ash, 10 parts of limestone powder, 14 parts of polystyrene particles, 10 parts of bentonite, 4 parts of thickener, 6 parts of double fly powder, 5 parts of thickener, 3 parts of carboxyethyl methylcellulose, 1.2 parts of sodium lauryl sulfate, 13 parts of calcium fluoride, 15 parts of styrene-maleic anhydride copolymer, 26 parts of sodium carbonate , 6 parts of hydrochloric acid.
[0025] The thickener is cellulose ether;
[0026] Described tackifier is ethylene-vinyl acetate copolymer latex powder;
[0027] The molar concentration of described hydrochloric acid is 3mol / L;
[0028] The preparation method of described thermal insulation mortar, comprises the following steps:
[0029] S1: Mix Portland cement, fly ash, limestone powder, polystyrene granules, bentonite, thickener, double fly powder, thickener, carboxyethyl methyl cellulose...
Embodiment 2
[0033] A kind of thermal insulation mortar, which comprises the following raw materials in parts by weight: 96 parts of Portland cement, 5 parts of fly ash, 12 parts of limestone powder, 15 parts of polystyrene particles, 9 parts of bentonite, 5 parts of thickener, 4 parts of double fly powder, 6 parts of thickening agent, 2 parts of carboxyethyl methyl cellulose, 0.8 parts of sodium lauryl sulfate, 14 parts of calcium fluoride, 16 parts of silicone-polyurethane copolymer, 22 parts of sodium carbonate, 7 parts of hydrochloric acid.
[0034] The thickener is cellulose ether;
[0035] Described tackifier is ethylene-vinyl acetate copolymer latex powder;
[0036] The molar concentration of described hydrochloric acid is 2mol / L;
[0037] The preparation method of described thermal insulation mortar, comprises the following steps:
[0038] S1: Mix Portland cement, fly ash, limestone powder, polystyrene granules, bentonite, thickener, double fly powder, thickener, carboxyethyl me...
Embodiment 3
[0042] A thermal insulation mortar, in parts by weight, comprising the following raw materials: 120 parts of Portland cement, 10 parts of fly ash, 6 parts of limestone powder, 10 parts of polystyrene particles, 12 parts of bentonite, 3 parts of thickener, 7 parts of double fly powder, 4 parts of thickener, 4 parts of carboxyethyl methylcellulose, 1.5 parts of sodium lauryl sulfate, 12 parts of calcium fluoride, styrene maleic anhydride copolymer or silicone-polyurethane copolymer 10 parts, 28 parts of sodium carbonate, 8 parts of hydrochloric acid.
[0043] The thickener is cellulose ether;
[0044] Described tackifier is ethylene-vinyl acetate copolymer latex powder;
[0045] The molar concentration of described hydrochloric acid is 4mol / L;
[0046] The preparation method of described thermal insulation mortar, comprises the following steps:
[0047] S1: Mix Portland cement, fly ash, limestone powder, polystyrene granules, bentonite, thickener, double fly powder, thickener...
PUM
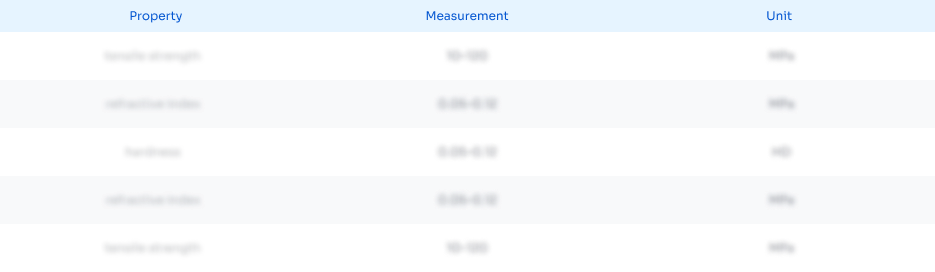
Abstract
Description
Claims
Application Information

- Generate Ideas
- Intellectual Property
- Life Sciences
- Materials
- Tech Scout
- Unparalleled Data Quality
- Higher Quality Content
- 60% Fewer Hallucinations
Browse by: Latest US Patents, China's latest patents, Technical Efficacy Thesaurus, Application Domain, Technology Topic, Popular Technical Reports.
© 2025 PatSnap. All rights reserved.Legal|Privacy policy|Modern Slavery Act Transparency Statement|Sitemap|About US| Contact US: help@patsnap.com