Multifunctional oil cutting fluid for metal finish machining and preparation method thereof
A multi-functional, cutting fluid technology, applied in the field of metal finishing, can solve problems such as product cleaning difficulties, workers' skin allergies, and serious oil mist in the workshop, and achieve the effects of favorable processing operations, simple preparation methods, and good oxidation resistance
- Summary
- Abstract
- Description
- Claims
- Application Information
AI Technical Summary
Problems solved by technology
Method used
Examples
example 1
[0030] S1: Take 10kg of base oil 150N by weight percentage and add it to the stirring tank, then add 1kg of high molecular weight polymer ester sulfide extreme pressure agent, 2kg of high alkali value calcium sulfonate, and 0.2kg of di-tert-butyl p-formaldehyde phenol.
[0031] S2: Turn on the agitator with a rotation speed of about 60r / min, and start the heating function at the same time. When the temperature of the material rises to 70~100°C, stir at a constant temperature for 30 minutes, and then turn off the heating function.
[0032] S3: Weigh 86.8kg of base oil 150N into the stirring tank, and continue stirring for 30 minutes to obtain 100kg of metalworking fluid.
example 2
[0034] S1: Weigh 10kg of base oil 150N into the stirring tank, add 2kg of high-molecular polymer ester sulfide extreme pressure agent, 2kg of high-molecular-weight ester polymer, and 0.2kg of di-tert-butyl-p-cresol.
[0035] S2: Turn on the stirrer at 60r / min, and start the heating function at the same time. When the temperature of the material rises to 70~100°C, stir at a constant temperature for 30min, and then turn off the heating function.
[0036] S3: Weigh 85.8kg of base oil 150N and put it into a stirring tank, and stir at room temperature for 30 minutes to obtain a metalworking fluid.
[0037] During the use of this metalworking fluid, there is no reaction on the production line and there are problems of irritating smell or skin irritation. For high-speed cutting aluminum alloy, stainless steel, and brass products, the life of the tool and the yield of the product can reach the same level as the purchased product. equivalent effect of metalworking fluids.
example 3
[0039] S1: Weigh 10kg of base oil 150N into the stirring tank, add 3kg of high-molecular polymer ester sulfide extreme pressure agent, 4kg of high-molecular-weight ester polymer, 0.2kg of di-tert-butyl-p-cresol, 0.2kg high molecular weight mixed esters.
[0040] S2: Turn on the stirrer at 60r / min, and start the heating function at the same time. When the temperature of the material rises to 70~100°C, stir at a constant temperature for 30min, and then turn off the heating function.
[0041] S3: Weigh 82.6kg of base oil 150N and put it into a stirring tank, then add all the concentrated solution prepared above, and stir at room temperature for 30 minutes to obtain 100kg of metalworking fluid.
PUM
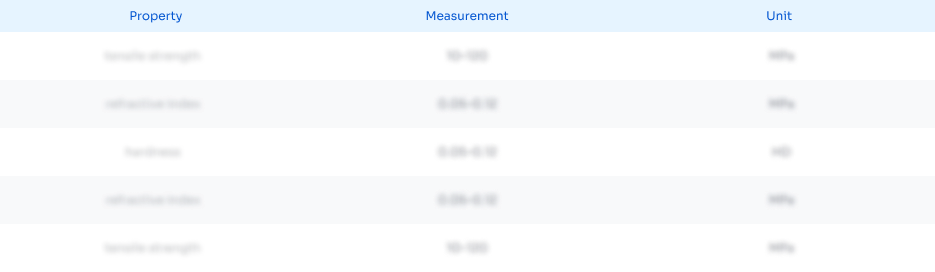
Abstract
Description
Claims
Application Information

- R&D Engineer
- R&D Manager
- IP Professional
- Industry Leading Data Capabilities
- Powerful AI technology
- Patent DNA Extraction
Browse by: Latest US Patents, China's latest patents, Technical Efficacy Thesaurus, Application Domain, Technology Topic, Popular Technical Reports.
© 2024 PatSnap. All rights reserved.Legal|Privacy policy|Modern Slavery Act Transparency Statement|Sitemap|About US| Contact US: help@patsnap.com