Method for preparing Ti2AlNb base alloy through powder metallurgy
A powder metallurgy and base alloy technology, applied in the field of titanium alloy preparation, can solve the problems of large difference in interdiffusion rate, poor sintering performance, high equipment requirements, etc., achieve good room temperature and high temperature mechanical properties, excellent powder sintering performance, and shorten the preparation process The effect of the process
- Summary
- Abstract
- Description
- Claims
- Application Information
AI Technical Summary
Problems solved by technology
Method used
Image
Examples
Embodiment 1
[0022] Embodiment 1: prepare 50Kg Ti-23Al-17Nb (at%) alloy sintered ingot
[0023] 1. Put 28.5Kg of sponge titanium and 20.7Kg of aluminum-niobium alloy (Nb: 0.75wt%, Al: 0.25wt%) into the hydrogenation furnace, heat the temperature to 450°C, and feed high-purity hydrogen to 0.05-0.1MPa for hydrogenation Processing 12h;
[0024] 2. Under the protection of argon, the material after hydrogenation treatment is ball milled and crushed, and the particle size of the powder after airflow classification is D50 = 10m;
[0025] 3. Add 0.8Kg elemental aluminum powder and mix for 2-10 hours, then put it into the dehydrogenation furnace, heat to 800°C, and keep it warm for 12 hours;
[0026] 4. Put the dehydrogenated powder into a rubber sheath for static pressure molding, the pressure is 200MPa;
[0027] 5. Put the compact after cold isostatic pressing into a vacuum sintering furnace for sintering, the maximum sintering temperature is 1250°C, and the holding time is 2h.
Embodiment 2
[0028] Embodiment 2: prepare 100Kg Ti-22Al-24Nb (at%) alloy sintered ingot
[0029] 1. Put 48Kg of sponge titanium and 48.2Kg of aluminum-niobium alloy (Nb: 0.85wt%, Al: 0.15wt%) into the hydrogenation furnace, heat the temperature to 500°C, and feed high-purity hydrogen to 0.1-0.15MPa for hydrogenation treatment 12h;
[0030] 2. Under the protection of argon, the material after hydrogenation treatment is ball milled and crushed, and the particle size of the powder after airflow classification is D50 = 10m;
[0031] 3. Add 3.8Kg elemental aluminum powder and mix for 2-10 hours, then put it into the dehydrogenation furnace, heat to 850°C, and keep it warm for 15 hours;
[0032] 4. Put the dehydrogenated powder into a rubber sheath for static pressure molding, the pressure is 200MPa;
[0033] 5. Put the compact after cold isostatic pressing into a vacuum sintering furnace for sintering, the maximum sintering temperature is 1300°C, and the holding time is 4h.
PUM
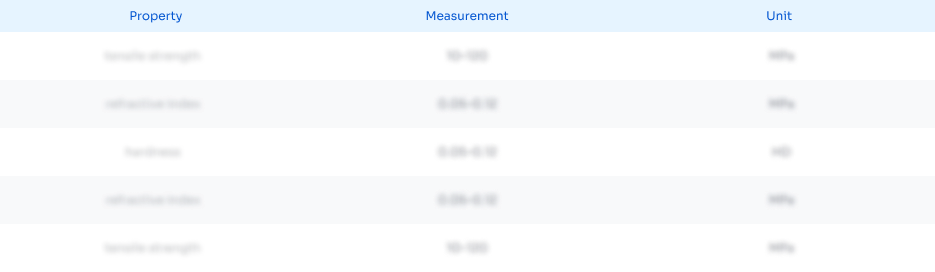
Abstract
Description
Claims
Application Information

- R&D
- Intellectual Property
- Life Sciences
- Materials
- Tech Scout
- Unparalleled Data Quality
- Higher Quality Content
- 60% Fewer Hallucinations
Browse by: Latest US Patents, China's latest patents, Technical Efficacy Thesaurus, Application Domain, Technology Topic, Popular Technical Reports.
© 2025 PatSnap. All rights reserved.Legal|Privacy policy|Modern Slavery Act Transparency Statement|Sitemap|About US| Contact US: help@patsnap.com