Catalyst for synthesizing higher branched alcohols, preparation method and application
A technology for catalysts and branched alcohols, which is applied in the preparation of organic compounds, chemical instruments and methods, and the preparation of hydroxyl compounds. It can solve problems such as the mismatch of active centers on catalysts, and achieve high conversion rates of raw material alcohols, low production costs, and The effect of easy product separation
- Summary
- Abstract
- Description
- Claims
- Application Information
AI Technical Summary
Problems solved by technology
Method used
Examples
Embodiment 1
[0032] Weigh 1.8g of copper nitrate hexahydrate, 128.2g of magnesium nitrate hexahydrate, 0.5g of zinc nitrate hexahydrate, 4.0g of 25wt% acidic silica sol and dissolve in 1050mL of deionized water to obtain a solution A with a total metal ion concentration of 0.5M. Prepare 1.0M ammonia water B and 3.0M urea aqueous solution C respectively. Under stirring at 40° C., solution B was added to solution A until the pH value in the solution reached 6.0, then the addition of solution B was stopped, and stirring was continued for 6 h. The solution obtained above was added to 700 mL of solution C, mixed evenly, added to an autoclave, and subjected to hydrothermal treatment at 100° C. for 12 hours. The precipitate obtained after hydrothermal treatment was filtered, washed 4 times with deionized water, dried at 90°C for 24h, and calcined at 600°C for 4h. The mass composition of the obtained catalyst was MgO:CuO:SiO 2 : ZnO=100:3:5:1.
[0033] Apply above-mentioned catalyzer to tubular ...
Embodiment 2
[0035]Weigh 2.1 g of copper nitrate hexahydrate, 128.2 g of magnesium nitrate hexahydrate, 26.5 g of aluminum nitrate nonahydrate, and 1.2 g of zinc nitrate hexahydrate and dissolve in 586 mL of deionized water to obtain solution A with a total concentration of metal ions of 1M. Prepare 1.0M ammonia water B and 1.0M urea aqueous solution C respectively. Under stirring at 60°C, solution B was added to solution A until the pH value in the solution reached 6.5, then the addition of solution B was stopped and stirring was continued for 2 hours. The solution obtained above was added to 600 mL of solution C, mixed evenly, added to an autoclave, and hydrothermally treated at 120° C. for 8 hours. The precipitate obtained after hydrothermal treatment was filtered, washed 5 times with deionized water, dried at 100°C for 16 hours, and calcined at 550°C for 4h. The mass composition of the obtained catalyst was MgO:CuO:Al 2 o 3 : ZnO=100:3.5:18:2.5.
[0036] Apply the above catalyst to ...
Embodiment 3
[0038] Weigh 2.4g of copper nitrate hexahydrate, 128.2g of magnesium nitrate hexahydrate, 4.0g of titanyl sulfate, and 3.5g of ferric nitrate nonahydrate and dissolve them in 363mL of deionized water to obtain a solution A with a total concentration of metal ions of 1.5M. Prepare 1.0M ammonia water B and 1.0M urea aqueous solution C respectively. Under stirring at 55°C, solution B was added to solution A until the pH value of the solution reached 7.0, then the addition of solution B was stopped, and stirring was continued for 3 hours. The solution obtained above was added to 470 mL of solution C, mixed evenly, added to an autoclave, and subjected to hydrothermal treatment at 80° C. for 16 hours. The precipitate obtained after hydrothermal treatment was filtered, washed 6 times with deionized water, dried at 120°C for 10h, and calcined at 600°C for 4h. The mass composition of the obtained catalyst was MgO:CuO:TiO 2 : Fe 2 o 3 =100:4:10:3.5.
[0039] Apply above-mentioned ca...
PUM
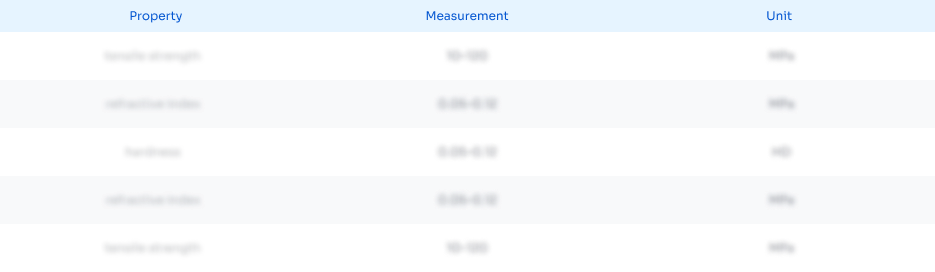
Abstract
Description
Claims
Application Information

- R&D Engineer
- R&D Manager
- IP Professional
- Industry Leading Data Capabilities
- Powerful AI technology
- Patent DNA Extraction
Browse by: Latest US Patents, China's latest patents, Technical Efficacy Thesaurus, Application Domain, Technology Topic, Popular Technical Reports.
© 2024 PatSnap. All rights reserved.Legal|Privacy policy|Modern Slavery Act Transparency Statement|Sitemap|About US| Contact US: help@patsnap.com