Powder dispersion method for magnetron sputtering coating
A magnetron sputtering coating and magnetron sputtering technology, applied in the field of powder dispersion, can solve the problems of small particle size, large specific surface area and large surface energy of powder materials, and achieve uniform coating, uniform dense film, The effect of reducing the surface energy
- Summary
- Abstract
- Description
- Claims
- Application Information
AI Technical Summary
Problems solved by technology
Method used
Examples
Embodiment 1
[0019] Take 500g of 100-150μm glass flakes and mix them with 25g of 1mm-2mm quartz sand evenly, put them into the storage bin of the magnetron sputtering coating machine, and assemble a cylindrical aluminum target on the magnetron sputtering target. Close the door of the vacuum chamber, turn on the vacuum pumping system, and evacuate to 4.3×10 -3 Pa, 50sccm of argon gas with a purity of 99.999% is introduced, and the vacuum degree of the cavity is controlled at 1.5×10 -1 Pa, turn on the vibration motor, turn on the magnetron sputtering power supply, and perform magnetron sputtering aluminum plating on the mixed powder. After the sputtering is completed, turn off the sputtering power supply and vacuum system, open the chamber to the atmosphere, open the chamber door, take out the mixed powder, and sieve out the quartz sand to obtain aluminized artificial glass.
Embodiment 2
[0024] Take 400g of 50-75μm aluminum oxide powder and 45g of 500μm-1000μm solid glass beads and mix evenly, add it to the storage bin of the magnetron sputtering coating machine, and assemble the sheet-shaped copper target on the magnetron sputtering target. Close the door of the vacuum chamber, turn on the vacuum pumping system, and evacuate to 4.3×10 -3 Pa, 50sccm of argon gas with a purity of 99.999% is introduced, and the vacuum degree of the cavity is controlled at 1.5×10 -1 Pa, turn on the ultrasonic vibration, turn on the magnetron sputtering power supply, and perform magnetron sputtering copper plating on the mixed powder. After the sputtering is completed, turn off the sputtering power supply and vacuum system, open the chamber to the atmosphere, open the chamber door, take out the mixed powder, and sieve out the solid glass beads to obtain copper-plated aluminum oxide.
Embodiment 3
[0026] Take 300g of 20-40μm quartz sand and 50g of 250μm-800μm calcite, mix evenly, add it to the storage bin of the magnetron sputtering coating machine, and assemble a cylindrical titanium target on the magnetron sputtering target. Close the door of the vacuum chamber, turn on the vacuum pumping system, and evacuate to 4.3×10 -3 Pa, 50sccm of argon gas with a purity of 99.999% is introduced, and the vacuum degree of the cavity is controlled at 1.5×10 -1 Pa, turn on the vibration motor, turn on the magnetron sputtering power supply, and perform magnetron sputtering titanium plating on the mixed powder. After the sputtering is completed, turn off the sputtering power supply and vacuum system, open the chamber to the atmosphere, open the chamber door, take out the mixed powder, and sieve out the calcite to obtain titanium-coated quartz sand.
PUM
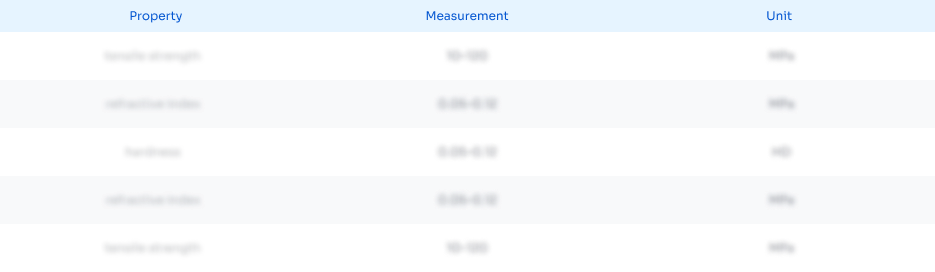
Abstract
Description
Claims
Application Information

- R&D Engineer
- R&D Manager
- IP Professional
- Industry Leading Data Capabilities
- Powerful AI technology
- Patent DNA Extraction
Browse by: Latest US Patents, China's latest patents, Technical Efficacy Thesaurus, Application Domain, Technology Topic, Popular Technical Reports.
© 2024 PatSnap. All rights reserved.Legal|Privacy policy|Modern Slavery Act Transparency Statement|Sitemap|About US| Contact US: help@patsnap.com