Self-repairing three-dimensional carbon fiber/memory alloy aircraft shell layer and preparation method thereof
A memory alloy and carbon fiber technology, which is applied to the field of self-healing three-dimensional carbon fiber/memory alloy aircraft shell and its preparation, can solve the problems of reduced bearing capacity, layered splitting of composite materials, and increased difficulty in recovery of composite materials, so as to improve the bearing capacity. ability, the effect of relieving internal stress and reducing internal defects
- Summary
- Abstract
- Description
- Claims
- Application Information
AI Technical Summary
Problems solved by technology
Method used
Image
Examples
Embodiment 1
[0025] (1) T700 carbon fiber is used as the weft yarn, the wavy nickel-titanium memory alloy is used as the warp yarn, and a three-dimensional angular interlocking structure is adopted. The warp yarn is interwoven with the weft yarn every two layers in the thickness direction, and a three-dimensional angular interlocking with a volume fraction of 45% is prepared. Base fabric, wherein the content of carbon fiber in the three-dimensional corner interlocking base fabric is not less than 60%.
[0026] (2) Immerse the three-dimensional angular interlocking base fabric in an electrolyte solution with a concentration of 3 wt %, anodize for 2 minutes at a relative current density of 8 mA / g, wash and dry, and obtain an oxidized three-dimensional angular interlocking base fabric.
[0027] (3) After mixing the repairable epoxy resin modified by diphenylmethane bismaleimide and polyethersulfone according to the mass ratio of 2:5, put it into the mold, and spread the microcapsules containin...
Embodiment 2
[0029] (1) T700 carbon fiber is used as the weft yarn, the wavy nickel-titanium memory alloy is used as the warp yarn, and a three-dimensional angular interlocking structure is adopted. The warp yarn is interwoven with the weft yarn every two layers in the thickness direction, and a three-dimensional angular interlocking with a volume fraction of 50% is prepared. Base fabric, wherein the content of carbon fiber in the three-dimensional corner interlocking base fabric is not less than 60%.
[0030] (2) Immerse the three-dimensional angular interlocking base fabric in an electrolyte solution with a concentration of 5 wt %, anodize for 3 minutes at a relative current density of 10 mA / g, wash and dry, and obtain an oxidized three-dimensional angular interlocking base fabric.
[0031] (3) After mixing the repairable epoxy resin modified by diphenylmethane bismaleimide and polyethersulfone according to the mass ratio of 3:10, put it into the mold, and spread the microcapsules contain...
Embodiment 3
[0033] (1) T700 carbon fiber is used as the weft yarn, the wavy nickel-titanium memory alloy is used as the warp yarn, and a three-dimensional angular interlocking structure is adopted. The warp yarn is interwoven with the weft yarn every two layers in the thickness direction, and a three-dimensional angular interlocking with a volume fraction of 46% is prepared. Base fabric, wherein the content of carbon fiber in the three-dimensional corner interlocking base fabric is not less than 60%.
[0034] (2) Immerse the three-dimensional angular interlocking base fabric in an electrolyte solution with a concentration of 4 wt%, anodize it at a relative current density of 9mA / g for 2.5min, wash and dry, and obtain an oxidized three-dimensional angular interlocking base fabric.
[0035] (3) After mixing the repairable epoxy resin modified by diphenylmethane bismaleimide and polyethersulfone according to the mass ratio of 2.5:7, put it into the mold, and spread the microcapsules containin...
PUM
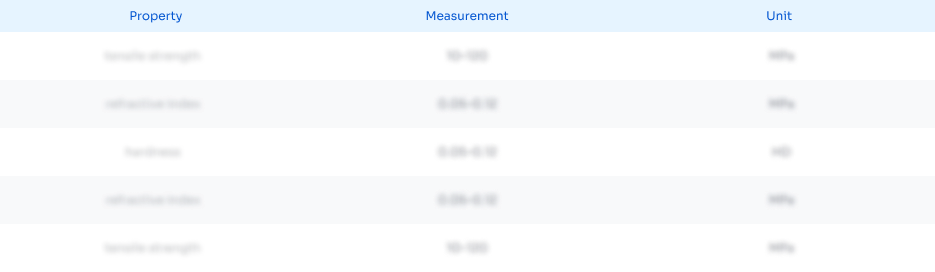
Abstract
Description
Claims
Application Information

- Generate Ideas
- Intellectual Property
- Life Sciences
- Materials
- Tech Scout
- Unparalleled Data Quality
- Higher Quality Content
- 60% Fewer Hallucinations
Browse by: Latest US Patents, China's latest patents, Technical Efficacy Thesaurus, Application Domain, Technology Topic, Popular Technical Reports.
© 2025 PatSnap. All rights reserved.Legal|Privacy policy|Modern Slavery Act Transparency Statement|Sitemap|About US| Contact US: help@patsnap.com