Organosilicone modified isocyanate prepolymer for solvent-free type synthetic leather and preparation method thereof
A technology of isocyanate prepolymerization and synthetic leather, which is applied in textiles and papermaking, etc. It can solve problems such as long curing time, inability to solve solvent pollution, and unsatisfactory air and moisture permeability, and achieve excellent flexibility, air permeability, and excellent hand feeling The effect of flexibility, excellent moisture permeability and air permeability
- Summary
- Abstract
- Description
- Claims
- Application Information
AI Technical Summary
Problems solved by technology
Method used
Image
Examples
Embodiment 1
[0022] (1) Weigh 100g of octamethylcyclotetrasiloxane and 61g of tetramethyltetraphenylcyclotetrasiloxane into a three-necked flask with a thermometer and a reflux device, N 2 Protect, warm up to 60℃, add 4.83g concentrated sulfuric acid, stir and react for 30min, add 7.5g tetramethyldihydrodisiloxane, stir and react at 60℃ for 5h, after the reaction, cool to room temperature, use carbonic acid Sodium hydrogen neutralizes the reaction solution to neutrality, washes with water, filters, and uses a rotary evaporator at 130°C to remove small molecular by-products, rotary evaporates for 4 hours, and filtered under reduced pressure to obtain a hydrogen end seal with a number average molecular weight of 3000 End methyl phenyl polysiloxane.
[0023] (2) Weigh 100g of the hydrogen-terminated methylphenyl polysiloxane obtained in step (1) and 3.8g of allylamine into the reactor, raise the temperature to 50°C, and add 0.001g of H 2 PtCl 6 The catalyst was reacted for 4h to prepare the amino...
Embodiment 2
[0026] (1) Weigh 100g of octamethylcyclotetrasiloxane and 57.5g of tetramethyltetraphenylcyclotetrasiloxane into the reactor, raise the temperature to 80°C, add 3.15g of concentrated sulfuric acid, and stir and react for 40min. Then 11.3g of tetramethyldihydrodisiloxane was added, and the reaction was stirred at 80℃ for 5h. After the reaction, the temperature was lowered to room temperature, neutralized with sodium oxycarbonate to neutrality, washed with water, filtered, and heated at 130 with a rotary evaporator. The small molecule by-products were removed by rotary evaporation at ℃, rotary evaporation for 4 hours, and vacuum filtration to prepare a hydrogen-terminated methylphenyl polysiloxane with a number average molecular weight of 2000.
[0027] (2) Weigh 100g of hydrogen-terminated methylphenyl polysiloxane and 5.7g of allylamine into the reactor, raise the temperature to 60°C, and add 0.002g of H 2 PtCl 6 The catalyst was reacted for 4h to prepare the amino-terminated meth...
Embodiment 3
[0030] (1) Weigh 100g octamethylcyclotetrasiloxane and 46g tetramethyltetraphenylcyclotetrasiloxane into the reactor, heat up to 75℃, add 4.38g concentrated sulfuric acid, stir and react for 30min, then add 22.6g tetramethyldihydrodisiloxane, stirred at 75℃ for 5h, after the reaction, cooled to room temperature, neutralized with sodium bicarbonate to neutrality, washed with water, filtered, and used a rotary evaporator at 130℃ Rotary steaming to remove small molecular by-products, rotating steaming for 4 hours, and filtering under reduced pressure to prepare a hydrogen-terminated methylphenyl polysiloxane with a number average molecular weight of 1000.
[0031] (2) Weigh 100g hydrogen-terminated methylphenyl polysiloxane and 7.6g allylamine into the reactor, heat up to 60°C, add 0.003g H 2 PtCl 6 The catalyst was reacted for 4h to prepare the amino-terminated methylphenyl polysiloxane.
[0032] (3) First, heat the amino-terminated methylphenyl polysiloxane obtained in step 2 to 120...
PUM
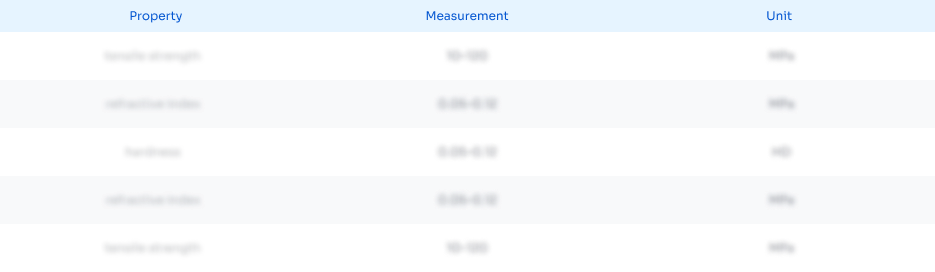
Abstract
Description
Claims
Application Information

- R&D
- Intellectual Property
- Life Sciences
- Materials
- Tech Scout
- Unparalleled Data Quality
- Higher Quality Content
- 60% Fewer Hallucinations
Browse by: Latest US Patents, China's latest patents, Technical Efficacy Thesaurus, Application Domain, Technology Topic, Popular Technical Reports.
© 2025 PatSnap. All rights reserved.Legal|Privacy policy|Modern Slavery Act Transparency Statement|Sitemap|About US| Contact US: help@patsnap.com