A kind of manufacturing method of polyester chip for heat shrinkable film
A polyester chip and production method technology, applied in the production field of copolymerized modified polyester, can solve the problems of many side reactions, slow esterification, large difference in thermal shrinkage properties, etc. Yellow, good heat shrinkage effect
- Summary
- Abstract
- Description
- Claims
- Application Information
AI Technical Summary
Problems solved by technology
Method used
Image
Examples
Embodiment 1
[0028] The present embodiment makes the polyester chips for heat-shrinkable film according to the following steps:
[0029] 1. Step by step beating process
[0030] High-temperature beating kettle: put 814kg of neopentyl glycol into the high-temperature beating kettle, slowly raise the temperature to 110°C, keep the temperature for 30 minutes, click to start the stirring motor, and slowly put in 1100kg of terephthalic acid, 3kg of p-toluenesulfonic acid, and 2kg of sodium acetate Stir well to combine.
[0031] Normal temperature beating kettle: Put 1720kg of ethylene glycol into the normal temperature beating kettle, start the stirring motor, slowly add 3650kg of terephthalic acid and 250kg of isophthalic acid, and fully stir evenly.
[0032] Step 2. Low-temperature step-by-step esterification
[0033] The first step of esterification: the material treated in the high-temperature beating tank is slowly and uniformly sent into the first esterification tank through a gear pump...
Embodiment 2
[0038] The manufacturing process of the polyester chip of this embodiment is identical with embodiment 1, and difference only is that step 1 is carried out as follows:
[0039] Put 1,720kg of ethylene glycol and 814kg of neopentyl glycol into the beating kettle and stir thoroughly, then slowly add 4,750kg of terephthalic acid, 250kg of isophthalic acid, 3kg of p-toluenesulfonic acid, and 2kg of sodium acetate. beating.
Embodiment 3
[0041] The manufacturing process of the polyester chips in this example is the same as that in Example 1, the only difference being that no compounding auxiliary agent is added.
PUM
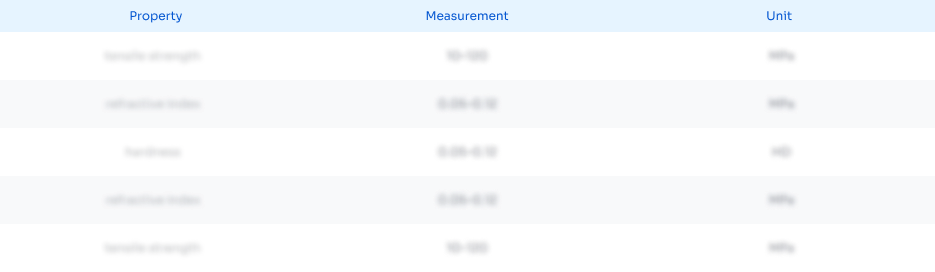
Abstract
Description
Claims
Application Information

- R&D Engineer
- R&D Manager
- IP Professional
- Industry Leading Data Capabilities
- Powerful AI technology
- Patent DNA Extraction
Browse by: Latest US Patents, China's latest patents, Technical Efficacy Thesaurus, Application Domain, Technology Topic, Popular Technical Reports.
© 2024 PatSnap. All rights reserved.Legal|Privacy policy|Modern Slavery Act Transparency Statement|Sitemap|About US| Contact US: help@patsnap.com